Eine der Hauptursachen für die Kontamination in der aseptischen Fertigung liegt beim Eingreifen des Bedieners. Daher führt die Reduzierung menschlicher Eingriffe in der kritischen Zone zu einer höheren Prozesssicherheit und somit Reinheit der Produkte. Zu einem gewissen Zeitpunkt wird sich jeder Pharmahersteller der endlosen Diskussion „RABS vs. Isolator“ stellen müssen. Um sicherzustellen, dass das Barrieresystem den Anforderungen des jeweiligen Produkts und der Anlage entspricht, ist es wichtig, die vorhandenen Möglichkeiten zu berücksichtigen. Die beiden gebräuchlichsten Barrieretechnologien, die von Pharmaunternehmen eingesetzt werden, sind Restricted Access Barrier Systeme (RABS) und Isolatoren.
RABS: Lösung mit Fokus auf flexibles Handling
RABS stellen eine physische Barriere zwischen dem Produktionsbereich und der Bedienerumgebung dar. Der Produktionsbereich wird durch eine spezielle Maschinenbeschutzung bestehend aus Maschinengehäuse, sicher verriegelte Türen und Eingriffe mit Handschuhen geschützt. Je nach Art der Belüftung können RABS in aktive und passive Systeme unterteilt werden. Aktive RABS sind mit speziellen Lüftungsanlagen ausgestattet, während passive RABS an der bestehenden Reinraumdecke des umgebenden B-Raums angeschlossen werden. Sie stellen eine attraktive Option für bestehende Reinräume zur Verbesserung der Produktionsqualität und für Anwendungen mit höheren Flexibilitätsanforderungen dar. Bei sachgemäßem Betrieb als integriertes System kann die RABS-Technologie die mikrobiologische Qualität eines Isolators erreichen. RABS müssen in der Regel manuell gereinigt und dekontaminiert werden. In den letzten Jahren sind immer häufiger Kombinationen mit automatisierten Systemen zur Raumdekontamination zu beobachten. Die größte Herausforderung für den Betrieb von RABS besteht jedoch darin, dass sie eine hochklassige Umgebung der Reinraumklasse B erfordern.
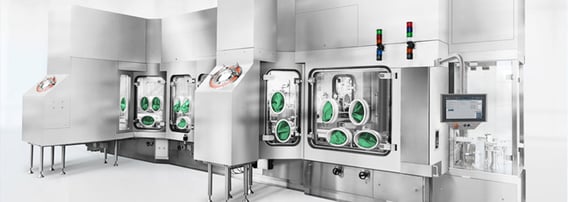
Isolatoren: Lösung mit höchster Sterilitätssicherheit
Ein Isolator wiederum ist ein vollständig geschlossenes System mit einer bestmöglichen Trennung von Bediener und Prozessbereich. Während der Produktion können die Türen nicht geöffnet werden. Pharmazeutische Isolatoren sind typischerweise mit einem vollständig reproduzierbaren und validierbaren System zur Biodekontamination (meist H2O2) und einer zugehörigen Prozesslüftungstechnik ausgestattet, die eine Temperaturregelung durch Heizen oder Kühlen sowie eine permanente Überdruckregelung des Prozessbereichs gegenüber der Bedienerumgebung gewährleistet, um das Eindringen von kontaminierter Luft zu vermeiden. Die reproduzierbare und validierte Dekontamination ist einer der Faktoren die es ermöglichen, Isolatoren in Umgebungsbedingungen der Klasse C oder D aufzustellen. Insbesondere die Zykluszeiten der Biodekontamination haben sich im Laufe der letzten Jahre enorm verbessert, um einen flexibleren Einsatz auch für Isolatoren zu ermöglichen.
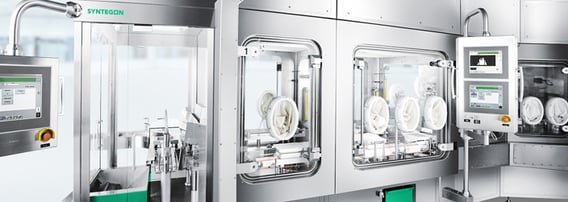
Mit unseren regelmäßigen News-Updates informieren wir Sie über Neuigkeiten zu Technologien und Services, Fallbeispielen, Webinarangeboten und Events.
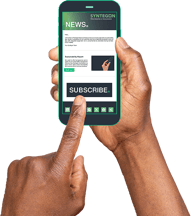
Vergleich von Isolatoren und RABS
Sowohl RABS- als auch Isolatorsysteme sind in der Pharmaindustrie mit Hunderten von Installationen weltweit etabliert. Beim Vergleich der beiden Barrieresysteme sind sowohl quantitative als auch qualitative Faktoren zu unterscheiden. In Bezug auf Kosten bieten RABS den Vorteil geringerer Investitionskosten. Andererseits sind die Betriebskosten (z.B. Reinraumkleidung, Reinraum Monitoring, etc.) im Vergleich zu Isolatorsystemen deutlich höher. Die anfängliche höhere Investition bei einem Isolatorsystem ist auf die integrierte Biodekontamination sowie sonstige Prozesstechnik auf höherem Niveau zurückzuführen.Um herauszufinden, welches Barrieresystem für Ihre Anwendung am besten geeignet ist und welche Technologien zur Erfüllung neuer regulatorischer Anforderungen benötigt werden, bedarf es eines zuverlässigen Partners mit umfangreicher Branchenkenntnis.
Syntegon, ehemals Bosch Packaging Technology, verfügt über mehr als 25 Jahre Erfahrung in der Herstellung von Isolatoren und kompletten Produktionslinien und besitzt zahlreiche weltweite Referenzen. Wir bieten Ihnen ein einmaliges Integrationskonzept – von der Füllmaschine bis zum Isolator selbst, über die Biokontaminations- und Lüftungstechnik bis hin zur Qualifizierung und Validierung des Gesamtsystems und umfassenden After-Sales-Service – alles aus einer Hand.