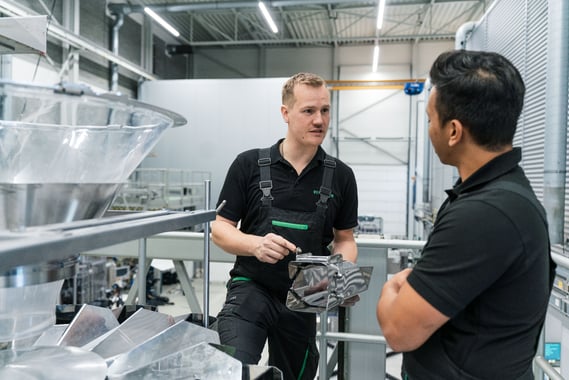
Service Agreements
Find out more about our Service Agreements here.
Processing and packaging machines for the food industry
We have supported food manufacturers with processing and packaging machines and equipment for more than 160 years. Our portfolio includes stand-alone food packaging machines and complete system solutions for the primary, secondary and tertiary packaging of food products such as bars, biscuits, bakery and frozen food, as well as processing technology for confectionery. With our packaging technologies with short changeover times to accommodate numerous pack styles, we are keeping up with changing consumer needs. As a leader in sustainable packaging solutions, we are striving to reduce the environmental impact of packaged food. Our global team of service experts ensures safe and reliable packaging processes.
The new SVX-series features a patent pending cross seal drive, providing the highest speeds in the industry. With an intuitive user interface plus a footprint so small, the SVX integrates seamlessly into new and existing packaging lines.
Learn more about the huge gain of linear motors (XTS) for high-performance packaging machines. Due to the increased high degree of flexibility demanded by our confectionery customers, we recognized the potential of XTS technology from Beckhoff early on.
What if food packaging could help preserve our planet? Let us challenge our view on conventional packaging – for a more sustainable world.
Confectionery and plastic flexibles go together like a horse and carriage – or at least they used to. Times are changing, and so are the materials that bars are wrapped in. Today, consumer goods companies are looking for more sustainable materials. Together with Mars Wrigley, we are investigating the flow wrapping potential of paper.
The robotic solution's camera-based vision control system detects products on the infeed belt. The delta robots pick single or multiple products arriving in random order and reliably place them in cartons, trays or other containers according to specifications.
Nestlé R&D in York has successfully shown how to switch their UK SMARTIES® tablet from conventional packaging to paper packaging: by approaching us and installing our new upgrade kit “paper-ON-form” on their existing flow wrappers.
The focus of our innovative packaging solutions is to preserve the unique aroma of coffee and its premium quality. We have developed valve technologies that allow a residual oxygen content of less than 1%, so none of coffee’s thousands aroma components are lost.
Suitable for sensitive food products featuring an easy detachment of the barrier layer and the lid.
Get inspired with regular updates on technologies and services, case studies, webinar offers and events.
Your cookies and crackers deserve the best handling and packaging solution.
Hygienic machine design and automation technologies, from primary to secondary packaging.
Latest insights on processing and packaging for a demanding product.
Hygienic, flexible packaging solutions including stand up bags like full corner seal or Doy.
The future of the coffee market and a checklist for long-term success.
Impact of the product characteristics of health and nutrition bars on the packaging process.
A guide through the maze of sustainable packaging solutions.
Find out more about our Service Agreements here.
Find out more about Digital Solutions here.
Find out more about Parts here.
Find out more about Maintenance here.
Find out more about Technical Support here.
Find out more about Modernizations here.
Find out more about our Training here.
Find out more about our Expert Services here.
Learn more about our sustainable coffee packaging solutions.
Uncover the secret to visually stunning biscuits, cookies, and crackers. Our site highlights the...
Learn how Syntegon empowers cookie and cracker producers to navigate industry challenges, including...
Discover the features of every biscuit, cookie, and cracker. From shapes to fillings, our expertise...
Discover innovative confectionery solutions at ProSweets 2025, booth D045, Hall 10.1. Experience...
It refers to a wide range of specialized equipment used in the food industry to package food safely, accurately, and hygienically. Packaging machinery automates packaging processes to increase production speed and efficiency. At the same time, it ensures that food is packaged in a way that extends shelf life, prevents contamination, and preserves food freshness.
Food packaging machinery comes in various types, each serving specific purposes in the packaging process. Common types include fillers for filling liquid food into containers, plastic bag and pouch sealers, primary packaging machines including vertical and horizontal form fill seal machines, vacuum packaging machines and cartoners as well as case packers to produce POS and shipping packages. In addition, there is upstream equipment like dosingand weighing technology, feeding solutions like robotic pick and place, inspection machines, conveyers, quality control systems and downstream equipment like palletizers. These packaging machines are often integrated into packaging line system solutions, working seamlessly together to efficiently package food. The choice of machinery depends on the specific packaging needs and characteristics of the food product and the targeted production volume.
Prioritizing safety features is crucial to prevent accidents, maintain the integrity of food products, and comply with regulatory standards. One aspect is hygienic machine design: providing easily cleanable surfaces that prevent the build-up of bacteria, using materials resistant to corrosion, and allowing easy disassembly for thorough cleaning. Other aspects are safety guards, interlocking systems, emergency stop buttons, proximity sensors and warning alarms, all aiming to reduce the risk of accidents for machine operators. Regular equipment and machinery maintenance, operator training, and adherence to safety protocols are equally important in ensuring a safe working environment.
When bagging or flow wrapping a food product, you can either apply modified atmosphere packaging (MAP) by adjusting gas compositions or apply vacuum packaging to reduceoxygen exposure inside the packaging. Both systems preserve food freshness and extend shelf life. Another crucial role plays seal integrity, as proper sealing methods like heat sealing prevent moisture ingress or microbial contamination. Overall, a hygienic packaging process including machinery designed with easy-to-clean surfaces is a must in order to reduce the risk of contamination during packaging. Food producers should also invest in quality control by implementing mechanisms to check for defects, thus ensuring accurate packaging with highquality standards.
Regulatory requirements for food packaging machines can vary by region and country, but several key standards and guidelines are commonly followed to ensure safety, hygiene, and compliance. Some of these include CE Marking (Europe), FDA Regulations (United States), ISO Standards, or Hazard Analysis and Critical Control Points (HACCP). Packaging equipment suppliers are often required to provide documentation, including manuals, safety instructions, and compliance certificates, demonstrating adherence to regulatory standards. Planned inspections and maintenance of packaging machines ensures continued compliance with regulatory standards.
Both regulatory pressure and public concerns around single-use plastic packaging waste are changing the way food is being packaged. Food producers are assessing their packaging equipment as one way to reduce their overall environmental impact. Key approaches of supporting more sustainable packaging are minimizing material consumption, investingin energy saving equipment, adapting pack sizes, and seeking out for renewable packaging materials.
When it comes to the selection of film packaging material, food manufacturers can opt for more environmentally friendly mono-material or paper alternatives. While processing paper for secondary and end-of-line packaging is well established, there is still much to explore in primary flexible packaging. From a machinery point of view, the transition is complex, as sealing parameters such as pressure, temperature and time need to be adjusted. As a pioneer in sustainable packaging, we are happy to share our know-how and adapt your food production to handling eco-friendly materials without compromising on production efficiency or product quality.
Learn more about our sustainable packaging solutions.