The customer is a US manufacturer of organic, plant-based food and ingredients. For their extruded fruit leather and bars, they required a second packaging line to package the increased production output.
Bars: Extruded Fruit Leather and Bars
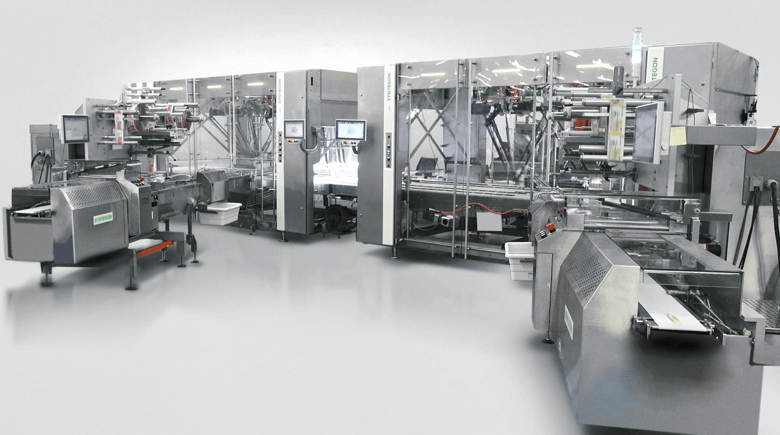
Project Description
The customer is a US manufacturer of organic, plant-based food and ingredients. For their extruded fruit leather and bars, they required a second packaging line to package the increased production output. The single flavor fruit leather is very thin and flexible. The multi-layer bar shape is very narrow. Both variants require special robotic handling capabilities. Floor space was limited. The new line had to be fitted next to the existing line, which was also supplied by Syntegon. This line is already in production.
Our Technical Solution:
- RPP’s vision system locates the bars’ position and orientation on the belt. The vision system tracks the products through the system to monitor their position.
- Four Delta robots per cell pick the bars from the belt and place them into the infeed chain of the Pack 403 flow wrapper.
- The infeed chain is mounted transversely at a 60° angle. This design allows for maximum product availability for the pick and place robots.
- Both Pack 403 flow wrapping machines wrap each product individually at speeds of 400 products per minute.
System Components:
- 1800 mm wide infeed conveyors for robots
- Two RPP 4-2 fitted with four delta robots in each cell
- The Delta robot arms are equipped with vacuum end-of-arm tools
- Two Syntegon Pack 403 flow wrappers
- Use of cold seal film
Output: 800 products per minute, 400 per flow wrapping machine.
The existing and the new packaging systems were seamlessly integrated in a confined production space.
- Same look and feel of the existing and new packaging lines. No additional operator training was necessary.
- Efficient use of floor space results in high output per m2.
- Reliable packaging of difficult to handle products.
- Future-proof packaging flexibility in terms of product, flavor mix and output.
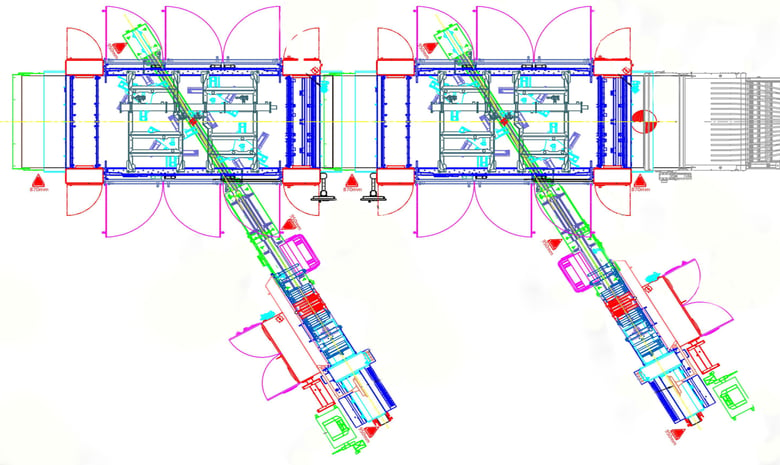
The customer is satisfied with the 1st installed line from Syntegon. The new system is fully integrated with the existing equipment in the same production space. The small footprint of the equipment helped to maximize the usage of the floor space.
The customer trusts in Syntegon’s proven product handling expertise. They were convinced by the overall line concept, combining existing and new equipment to a winning proposal. Syntegon equipment is designed and engineered to work as one seamless system. All components are benchmark technology.
Why choose a robotic system solution from Syntegon?
We offer turnkey solutions - including robotic application consultation and concept, engineering, installation and commissioning. Comprehensive operator training is available as well as local service through Syntegon's many service hubs around the world.
Syntegon is a market leader in seamless systems and the integration of different line components. With our broad portfolio of primary, secondary and tertiary packaging equipment, you will get tailored packaging solutions to reach your production goals. Future-proof flexibility is key regarding the choice of equipment. We always provide our customers with the best solution for today's production and future products or pack styles.
Our team of experts completed many projects and looks back at decades of application experience. Examples of reference lines for similar products are available on request.
For more information on robotic solutions from Syntegon, visit our website: Robotic packaging | Syntegon | Food processing automation
Download project
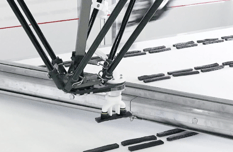
Robotic System Solution
Handling of oily and sticky fruit leather and extruded bars