Developing and manufacturing hard-shell capsules with low fill-weights can be an especially challenging task. However, recent innovations provide the tools to make the job of manufacturing such products much easier, while also providing assurance that the capsules you make meet your stringent quality requirements. Whether you need to fill just API into capsules for clinical trials, need to manufacture a low-fill capsule product for dry powder inhalation, or simply have a product formulation that requires low fill-weight, the tools available today can make the job much simpler.
Among the challenges of manufacturing capsules with low fill-weights is the delivery of small quantities of powder while maintaining tight weight tolerances. For example, a capsule product for dry-powder inhalation administration with a capsule fill-weight of 20 mg might have a tolerance of +/- 2 mg or less, depending upon manufacturer or regulatory requirements. With such low weights and tight tolerances, accurate filling and real-time weight confirmation are must-haves. With Syntegon’s micro-dosing technology, combined with our In-Process Control (IPC) system and Net Weight Detection System (NWDS), you can confidently manufacture low fill-weight capsules and analyze those capsules in real-time, helping you to achieve better quality and less waste.
At the heart of Syntegon’s micro-dosing technology is a vacuum dosing wheel capable of accurately dosing powder quantities as low as 500 µg at speeds as high as 156,000 capsules/hour. The vacuum dosing wheel gently transfers powder from hopper to capsule in a way that avoids creation of agglomerates, especially beneficial for inhaled powder administration. In addition, the vacuum dosing wheel technology doses in a way that leaves minimal powder waste at the end of a production run, helping you to achieve higher product yields.
Of course, confirmation that your capsules meet product specifications should be an integral part of your capsule filling process as well. The Net Weight Detection (NWDS) and In-Process Control (IPC) systems available on Syntegon’s GKF-720 and GKF-2600 capsule fillers provide assurance that each capsule manufactured has the quality attributes required.
Get inspired with regular updates on technologies and services, case studies, webinar offers and events.
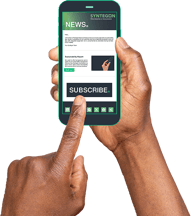
Through use of capacitive sensors located at the dosing station, the NWDS feature monitors the fill of each capsule produced, detecting any deviation in fill volume and automatically adjusting the machine to maintain target fill-weights. In conjunction with the NWDS, the IPC system gravimetrically establishes capsule fill-weights by determining both tare and gross weights of a sub-set of capsules sampled at a frequency determined by operating personnel. More important, during operation, the IPC system provides capsule-weight feedback to the NWDS, which utilizes this information to maintain precise calibration. Working together, the NWDS and IPC systems form a powerful tool that is an indispensable part of a robust capsule filling process.
If you currently have, or are developing a low fill-weight capsule product, you owe it to yourself to learn more about the sophisticated tools that Syntegon offers for manufacturing such products. For more information, visit our lineup of capsule fillers on our product page.