This year's CPHI Barcelona had many highlights to offer – especially at the Syntegon booth. The first presentation of our new Versynta microBatch turned out to be a real crowd puller. The gloveless production cell surprised visitors with both its numerous technological innovations and the sale of the very first machine to our development partner Vetter.
Following successful CPHI Barcelona: first Versynta microBatch goes to Vetter
This year's CPHI Barcelona had many highlights to offer – especially at the Syntegon booth. The first presentation of our new Versynta microBatch turned out to be a real crowd puller. The gloveless production cell surprised visitors with both its numerous technological innovations and the sale of the very first machine to our development partner Vetter.
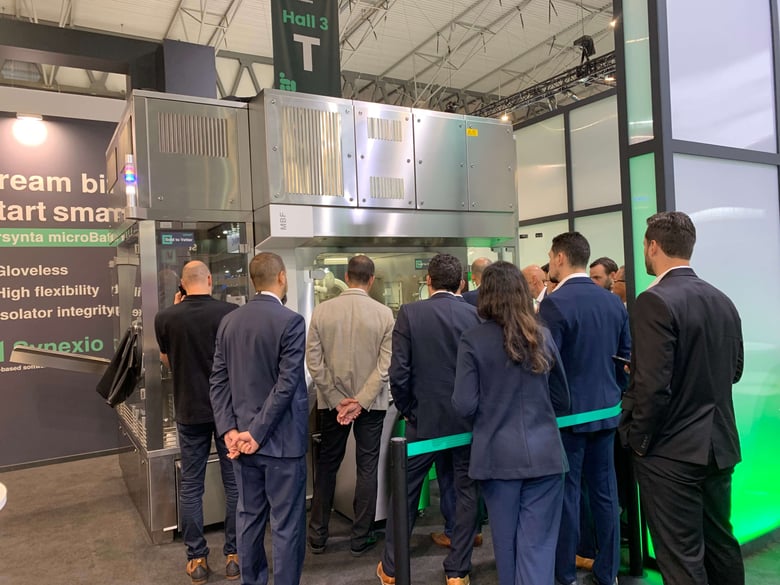
Focus on personal exchange
Finally, back at the heart of pharma! CPHI Barcelona once again lived up to its reputation as a networking and business platform. The focus of the trade show was on personal exchanges with pharmacists, API manufacturers, CDMOs, and machine builders from all over the world. The market launch of our Versynta microBatch quickly became the talk of the town. The Annex 1-compliant production cell with gloveless isolator and integrated air treatment sets new standards in aseptic filling – and has already won over its first customer.
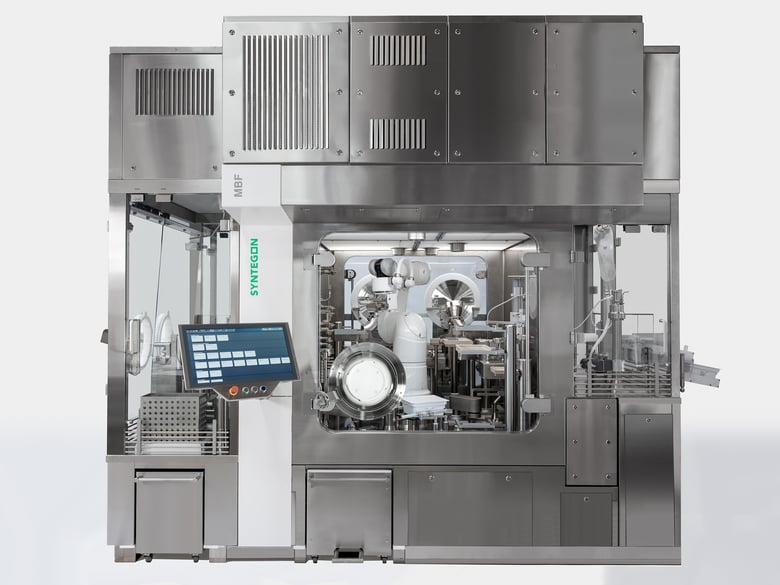
An award-winning cooperation
The first Versynta microBatch will be put into use at Vetter, a globally leading CDMO. “There was already a lively exchange between the experts on both sides during the development phase,” says Vetter Managing Director Thomas Otto. The development partnership was already honored with the PDA Drug Delivery Award in der category „Partnership Innovation“ in 2021, followed by the German Packaging Award a year later. “Versynta microBatch enables us to achieve the desired flexibility, regulatory compliance, and high level of automation that we, as one of the leading CDMOs in the fill and finish sector, want to offer our customers.”
The fully automated production cell fills between 120 and 500 containers per hour with virtually no product loss and 100% in-process control. The five integrated inline inspection systems provide particular safety. The requirements of the new Annex 1 were also taken into account during development: for example, the gloveless isolator with integrated air treatment significantly reduces the risk of contamination. Optional network cameras ensure continuous monitoring of production in the isolator via remote access.