In recent years, pharmaceutical manufacturers have developed and refined a wide range of antidiabetic drugs such as semaglutide and modern insulins, as demand is increasing rapidly.
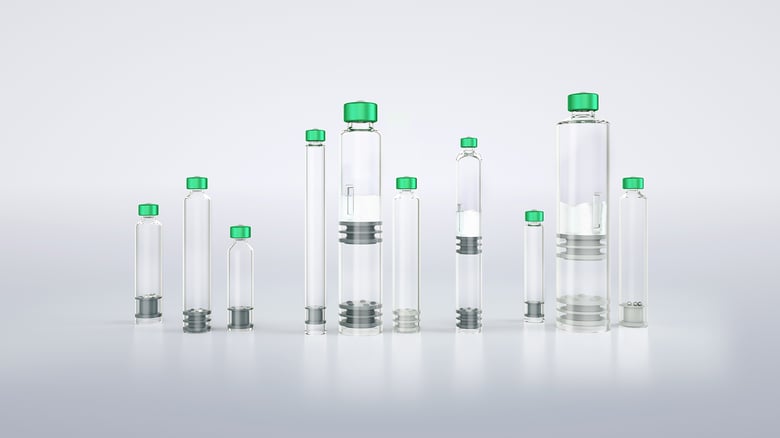
In recent years, pharmaceutical manufacturers have developed and refined a wide range of antidiabetic drugs such as semaglutide and modern insulins, as demand is increasing rapidly. Many enter the market as injectables in cartridges. Pharmaceutical companies use state-of-the-art inspection technology to keep pace with the high production volume and to reliably rule out contamination or defects in the container.
According to the International Diabetes Federation, 540 million people worldwide are currently living with diabetes, more than 90 percent of them suffer from type 2. This number will continue to rise in the future, which is why the focus is increasingly shifting to preventive treatment methods. The incretin mimetic semaglutide has gained popularity in recent years. The FDA approval of a high-dose injectable version in June 2021 (January 2022 in the European Union) has boosted demand. In addition, semaglutide-based drugs have now also been approved as anti-obesity medication for long-term weight management in adults. This way, they also preventively control one of the main risk factors for type 2 diabetes.
From static division to cameras and sensors
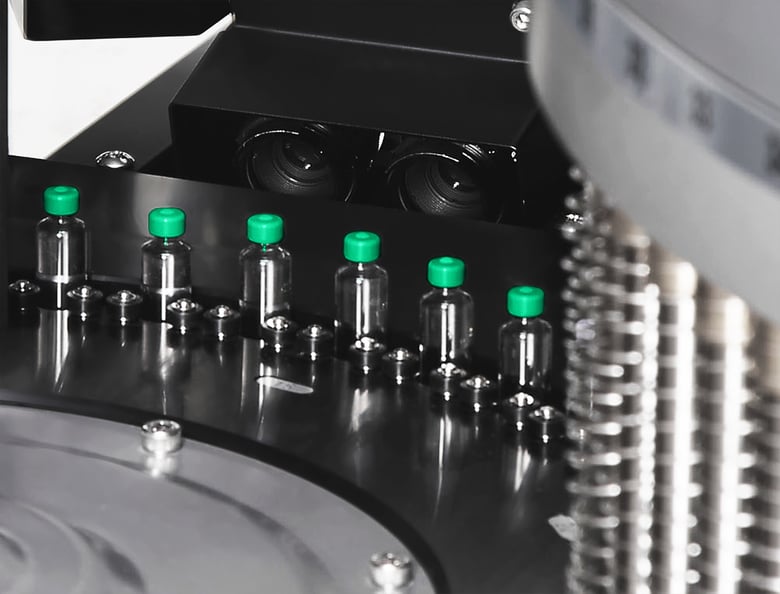
In diabetes treatment, pens equipped with cartridges have established themselves primarily due to their easy handling and relatively inexpensive production. The cartridges undergo numerous process steps during which they are exposed to fluctuating temperatures and stresses. This can lead to cracks, chips, or fractures. The product itself could also be contaminated. Modern inspection technology addresses all these points. One of the original methods of automatic inspection is the static division (SD) system.
Camera systems can be an alternative or add-on feature to SD inspection, for example to identify overly large air bubbles. Automatic inspection machines such as Syntegon’s AIM series are equipped with cameras that enable a side view of the cartridge stopper. Excessive pressure causes the septum of the stopper to bulge beyond the norm and the cartridge in question is automatically ejected. Cracks are often difficult to detect, especially at the neck of the cartridge. Automated camera systems that use the latest CCD and CMOS sensor technologies in combination with specially designed optics and LED lighting can provide a remedy.
Reliable closing thanks to CCIT
Many pharmaceutical manufacturers employ additional Container Closure Integrity Testing (CCIT) with High-Voltage Leak Detection (HVLD) to meet the increasingly stringent quality requirements. The filled cartridges are placed between electrode probes that apply high AC voltages of up to 30 kV. Intact and completely sealed cartridges yield only a small electric current signal. In contrast, conductive defect channels in the isolating barrier, even on the low end of the micrometer scale, cause increased signal. Thus, defective cartridges are reliably identified and ejected.
Flexibility meets safety
The already high demand for modern insulins, semaglutides, and other antidiabetics will continue to increase in the future. At the same time, treatments are becoming increasingly diversified. Syntegon’s state-of-the-art inspection technology helps pharmaceutical manufacturers to react quickly and flexibly to changing market requirements while ensuring the highest product quality.