Some customer inquiries are tough – and appear to be unsolvable at first. But with plenty of expertise and creativity, even tricky challenges can be overcome, as Janssen Vaccines Corporation and Syntegon have proven in their many years of successful cooperation.
Some customer inquiries are tough – and appear to be unsolvable at first. But with plenty of expertise and creativity, even tricky challenges can be overcome, as Janssen Vaccines Corporation and Syntegon have proven in their many years of successful cooperation.
As part of Janssen Pharmaceutical Companies of Johnson & Johnson, the Janssen Vaccines Corporation is pursuing an ambitious goal: treating, curing, and preventing some of the most devastating and complex diseases of our time, including diabetes, HIV, Covid-19, and cancer.
The Syntegon subsidiary Pharmatec has already implemented several demanding projects at the site in Incheon, South Korea since 2019. In 2020, the production site took an important strategic step: Janssen had to transfer processes from a European site to its Korean location to extend production for several new drug products.
A highly individualized system
The start for this long-term cooperation was the installation of a customized system by Pharmatec. It is situated on two levels and consists of a formulation system on the second floor, which mixes the products and transfers them to a storage tank located on the first floor. The tank feeds a vial filling machine from Syntegon.
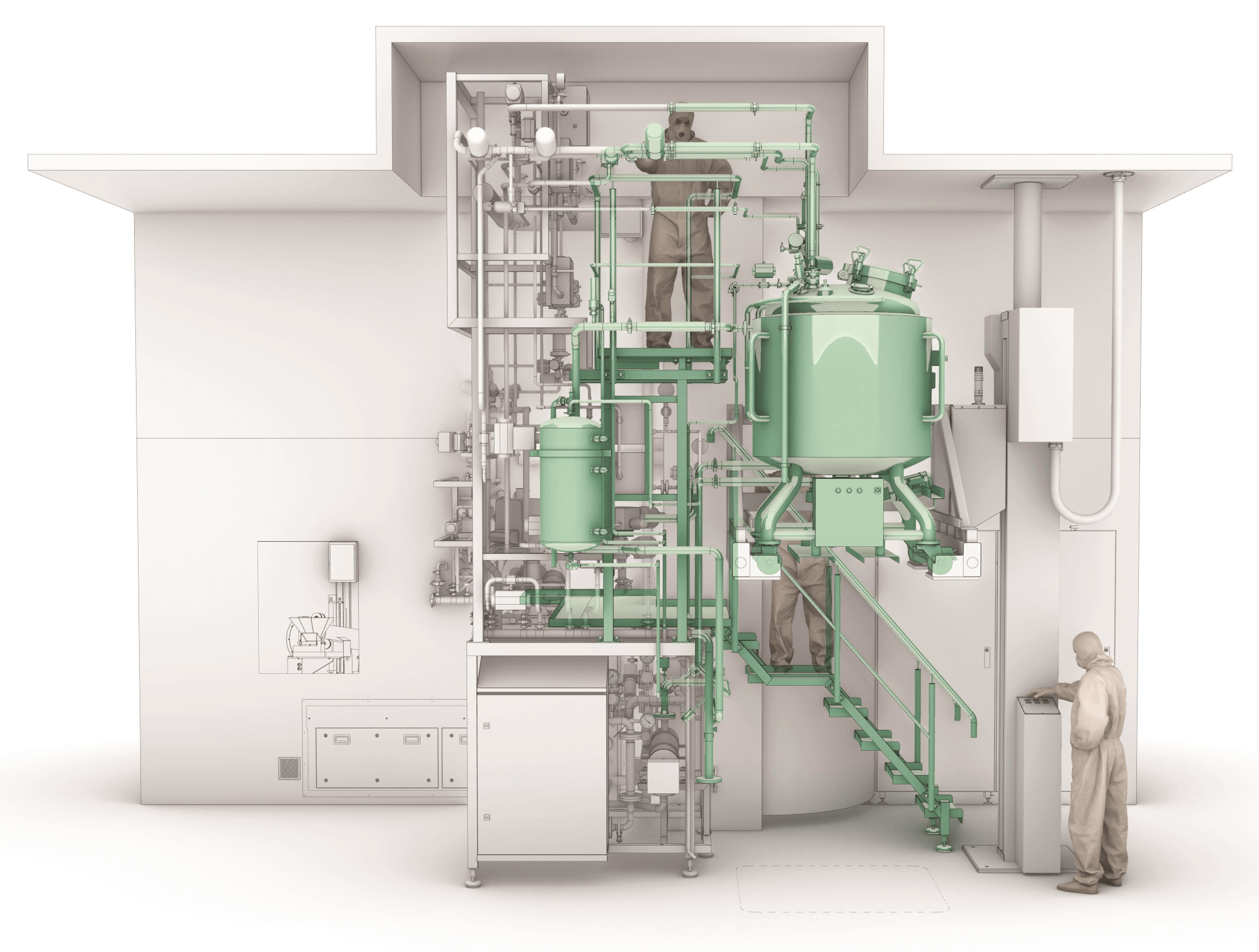
The system is highly individualized and unique from a technological and structural perspective.
A few years back, Janssen had to replace its old first-floor tank. In the wake of the patent expiration of its pediatric vaccine, the company had reoriented its production, adding vaccines and monoclonal antibodies for cancer treatment to its portfolio. This step required increasingly flexible manufacturing processes.
The Pharmatec experts installed a solution that enabled Janssen to maintain overall production while easily switching between different formulation volumes. Instead of a single tank on floor one, Janssen opted for two tanks that can be used flexibly depending on the desired manufacturing outputs: a 600-liter tank for large batches and a 150-liter variant for smaller production runs. Both containers can be readily connected to the vial filling machine from Syntegon.
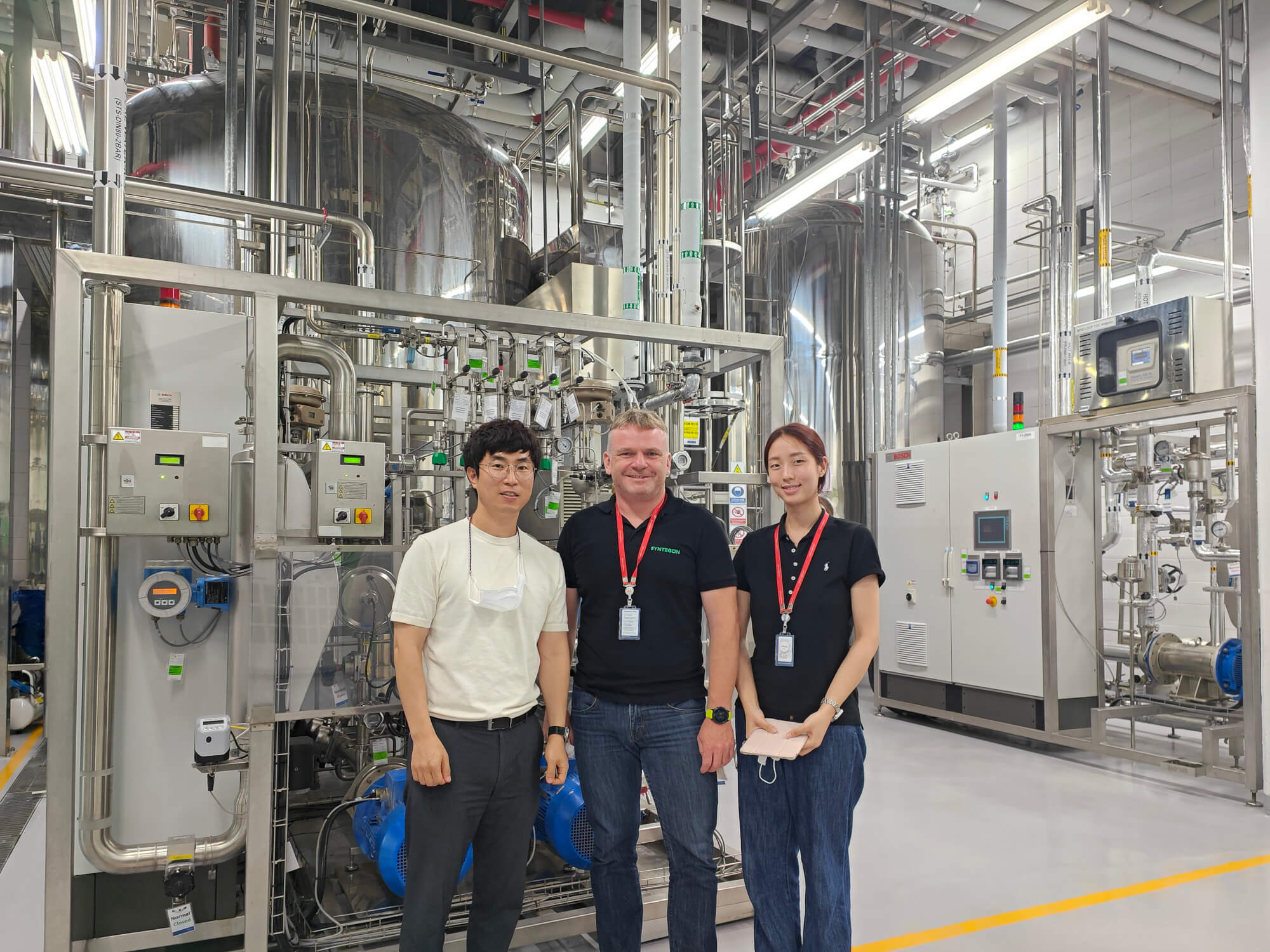
A talented team: the project members from Janssen Vaccines Corporation und Syntegon.
Lifting two containers proved to be a challenging yet rewarding project for the Pharmatec engineers. “Often, customer requests sound unusual or even unsolvable at first thought. But in the end, you can fulfil them with creativity, spontaneity, and technical knowledge,” says Martin Jäger, Pharmatec’s Senior Manager Sales Engineering and project manager in the modernization process. What started out as a modernization turned into a major opportunity for both project partners. “We realized that this was the right time to ramp up our flexible manufacturing readiness,” says Hae Eun Jeong, Project Engineer at Janssen.
To be continued
It goes without saying that the work never stops: Janssen and Syntegon are already planning the next steps. The Human-Machine-Interface (HMI) will receive an upgrade, and staff will be trained on the new equipment to ensure smooth operations from the very beginning.
Are you also planning a challenging project which you want to realize with an experienced partner? Contact us!