Whether they are made of aluminum or wood, or only exist virtually: machine models are essential for many pharmaceutical manufacturers and equipment suppliers to plan new filling lines in detail. This is also true for Syntegon: since 2007, the company’s Crailsheim site has created numerous concepts for customers – and is now continuing along the digital path.
Did you know that cars are made from clay before they can drive the streets and are ready for serial production? Car designers initially create full-sized models from malleable natural materials. Although Syntegon operates in a completely different industry, what applies to clay cars is also true for filling, packaging, or processing technology: in the beginning, nothing is cast in stone.
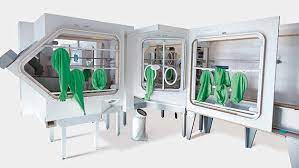
Syntegon Mock-up
Reproduction for press purposes free of charge with credit “Picture: Syntegon”
Working on and with models is part of daily business, especially for our German site in Crailsheim, where several of these so-called mock-up customer lines are built every year. “They help us harmonize future lines and customer needs,” says Matthias Angelmaier, product manager at Syntegon. During a mock-up, experts coordinate the height and design of glove ports or the number of particle and germ count with customers, and adapt their configurations, if required. “Our customers are involved in the design from start to finish,” says Angelmaier.
Models with tradition
Customers, Syntegon and suppliers have been frequently using the versatile opportunities of 3D models since 2007. Designers have always moved with the times: while aluminum was still predominantly used in the late 1980s, Syntegon has consistently been using wood since the 2000s – and now increasingly relies on digital twins. About ten years ago, the first analog model of the MLD filling and capping machine was equipped with virtual reality (VR) technology. AR glasses enabled customers to see technical details such as format or tool changes in real time.
What seemed new at the time is now daily business. Since the start of the pandemic, virtual solutions have been booming. However, this does not put an end to mock-ups. The Crailsheim team has developed its own model culture to offer customers an even larger choice, for example via a virtual live tour, using cameras and an online messenger. Customers can see the wooden model via video stream and discuss all the details online. Entirely virtual 3D models are also part of the company’s portfolio. They are used both for initial customer discussions and for Factory Acceptance Tests (FAT).
A wooden model in the canteen
Syntegon has already carried out several successful video FATs. The advantages of this method are manifold: while saving travel time and costs, customers get a good impression of their new line and can discuss any necessary adjustments with their Syntegon partners. The classic wooden model remains unaffected: “Every project is highly individual. Many customers still want to see and touch a model before we manufacture the line,” says Angelmaier. According to a Crailsheim anecdote, a customer even displayed his wooden model in the canteen.
No matter where you plan to display your machine model: in case we have drawn your interest to whatever kind of mock-up, our Crailsheim experts will be happy to help! Whether you are planning to install a new line or adapt existing equipment – we will meet your requirements with a Syntegon mock-up.