Even the best equipment eventually ages and some worn components are no longer available. In the worst case, production can come to a halt. Our service specialists inform you about this kind of risk – proactively and with the solution at hand. Their last trip took them to a customer in Slovenia.
Failures or wear of machine components are a frequent reason for production downtimes. This is particularly problematic if the necessary spare parts have already been discontinued by the manufacturer. Such a scenario is particularly delicate in the pharmaceutical industry, where life-saving products are often at stake. A costly procurement of replacements with long delivery times is out of the question. Therefore, our customers can rely on an "early warning system".
Recently, our colleagues from the Syntegon subsidiary Pharmatec travelled to a customer in Slovenia. "When we learned from our supplier that certain control valves would soon be discontinued, we acted immediately and informed our customer," says Pharmatec service technician Andreas Olzog. A distillation unit for the production of water for injection (WFI) and an ultra-pure steam generator were amongst the systems affected. The Slovenian customer has been relying on the Syntegon equipment for about 20 years – in 24/7 operations.
Future-proof thanks to the Pharmatec modernization service
To ensure that the equipment's last hour would not come anytime soon, Andreas Olzog's team proposed their own solutions for the discontinued wear parts. Having already replaced the HMI, it was now a matter of a total of five new control valves on two plants – which were replaced within just three days. "Thanks to the modernization, the Pharmatec systems are now equipped for several more years of continuous operation," Andreas Olzog confirms.
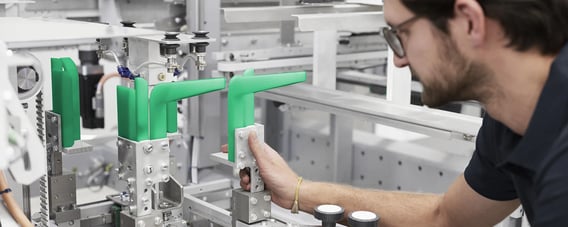
After the modernization service, this system is fit again for the next 20 years.
Reproduction for press purposes free of charge with credit “Picture: Syntegon”
Apart from the Pharmatec technician team and the Slovenian customer, pharmaceutical manufacturers who own older systems can also rejoice: Syntegon offers this modernization service to all existing customers: "In the meantime, we have established a fixed portfolio of spare parts and modernization services for our machines, which we are successively adapting," says Andreas Olzog. "So it's worth investing a little time in replacements to significantly increase the lifetime of the equipment."