Air handling in isolators takes up a considerable amount of space with boxy units and great lengths of piping. "In-air" isolators from Syntegon eliminate the need for traditional air handling solutions by integrating the technology into the plenum of the isolator.
Air handling in isolators takes up a considerable amount of space with boxy units and great lengths of piping. "In-air" isolators from Syntegon eliminate the need for traditional air handling solutions by integrating the technology into the plenum of the isolator.
Air handling technology plays an important role in the sterile production of pharmaceutical products. Traditional air handling units are an essential component of isolators that help to maintain the required temperature, humidity, and air flow conditions. Usually, these devices are positioned on the technical floors above the filling systems – and take up a lot of space. However, there are other options. Following the model of filling equipment for small batches that use integrated air handling technology, large commercial-scale production systems can now be equipped with "in-air" isolators.
Saving energy and space
Integrated air handling technology offers many advantages. The ventilation system pulls air required for the isolator from the surrounding class C room and exhausts it back into the clean room. This keeps the air balance neutral and has no effect on the ventilation system of the class C room. The bulky air handling units on the technical floor and the associated piping are also no longer required, as the coolers for temperature control are housed in the plenum of the isolator. This saves space on the technical floor above the filling system and reduces installation costs. In addition, in-air systems reduce energy consumption, as the air required in the isolator no longer has to be drawn in from the external environment and treated.
“We want to make life easier for manufacturers of large batches with integrated air handling," Lukas Munzinger, Product Manager at Syntegon, explains. “Our development enables them to produce in a space-saving and cost-efficient manner.”
A sophisticated process
The compact system comprising fans, cooling units, catalytic converters, and HEPA filters is located in the plenum of the filling line, directly on the isolator housing. Unlike external air treatment, the integrated version draws air directly from the clean room and returns it without the need for additional conditioning. This “room in/room out” principle enables resource saving recirculation of the HEPA-filtered air: the air drawn in via fans is maintained at 21 degrees Celsius, filtered, and distributed homogeneously in the isolator at a defined air speed of 0.45 m/s. Ventilation technology ensures a positive overpressure of 25 pascals to protect the aseptic production core in the class A environment. In addition, during the biodecontamination cycle, special catalyzers decompose the hydrogen peroxide (H2O2) used into clean water and oxygen. This allows in-air isolators to achieve the industry’s fastest biodecontamination times.
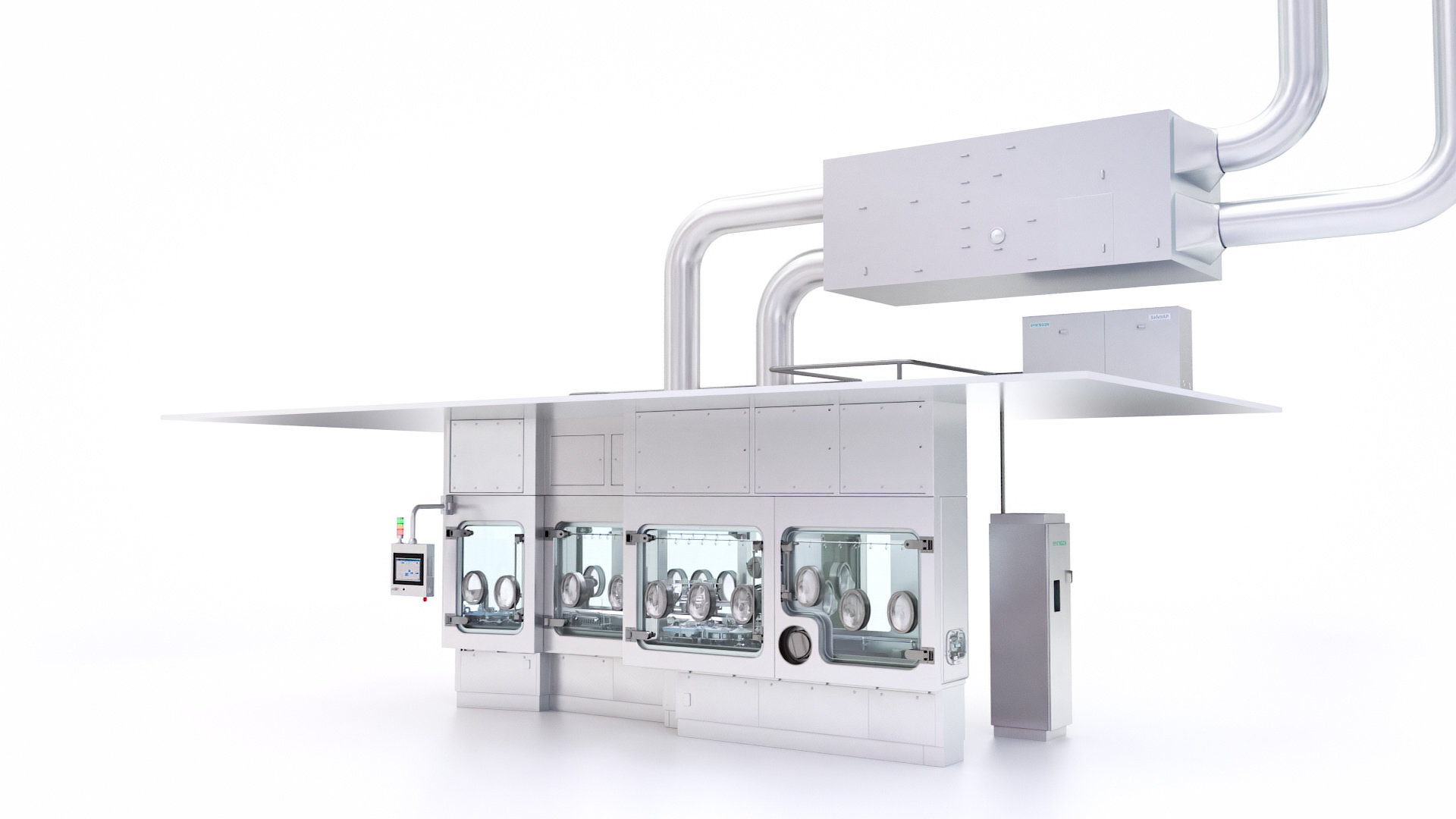
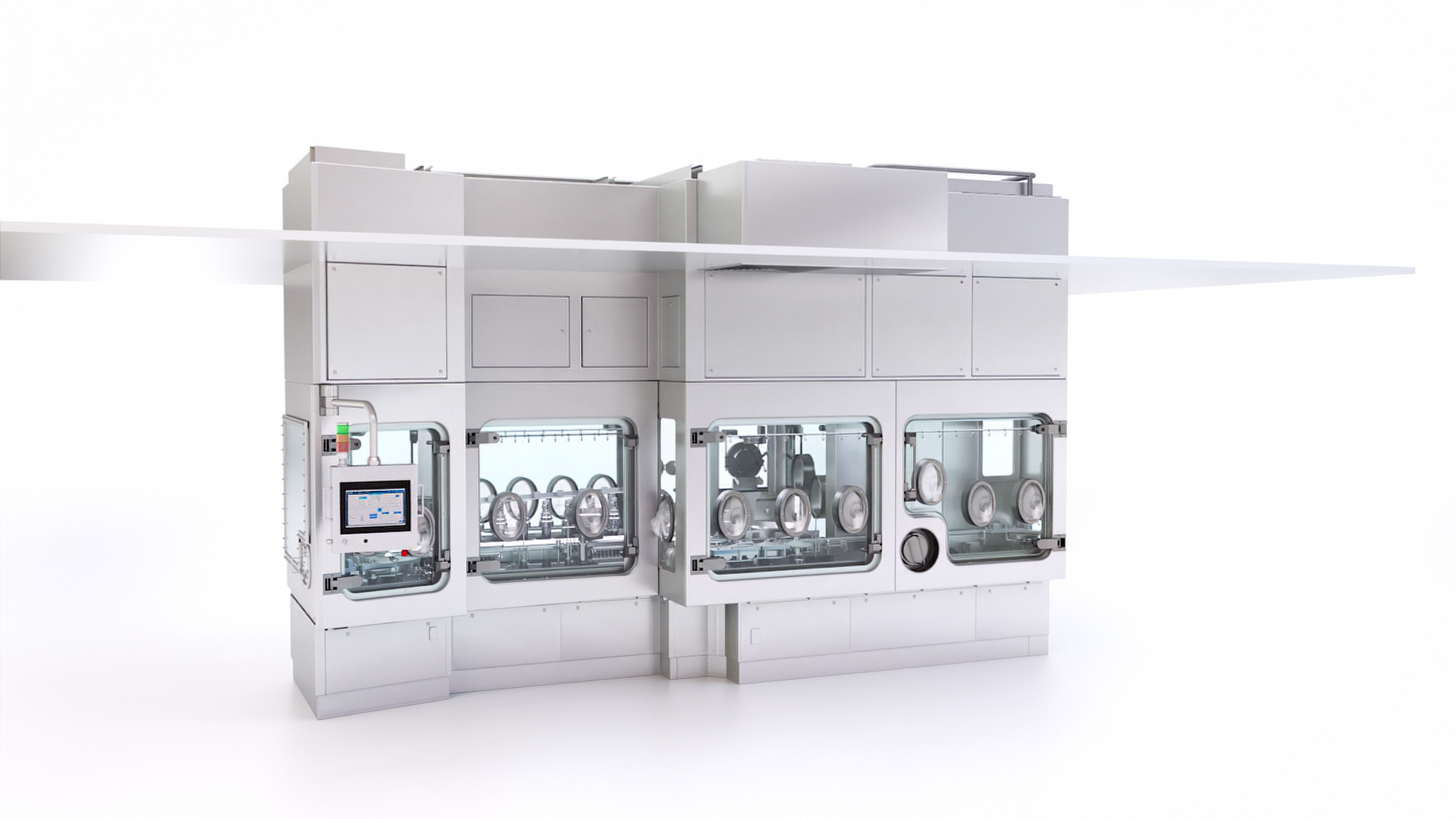
In contrast to external air treatment (left), the integrated in-air solution (right) requires only minimal space on the technical floor.
Get inspired with regular updates on technologies and services, case studies, webinar offers and events.
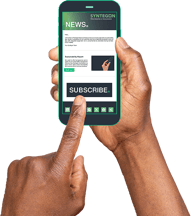
Simple set-up and reduced interfaces
“The very compact design of a filling system with integrated air handling technology simplifies numerous processes – from manufacturing the system to installing and commissioning it on premise,” Munzinger explains.
Eliminating all interfaces to the outside of the building not only benefits the team installing the system, but also the building planners – after all, their work becomes a lot easier. Eliminating outdoor air treatment also results in lower energy consumption for the entire system: the integrated air treatment makes it possible to run more sustainable processes. “In times of increased environmental requirements, our approach offers a significant energy advantage. For some large manufacturers, this should be a welcome incentive to use 'in-air' solutions in the future,” says Munzinger.
Does Syntegon’s integrated air handling sound intriguing? Contact us for more information.