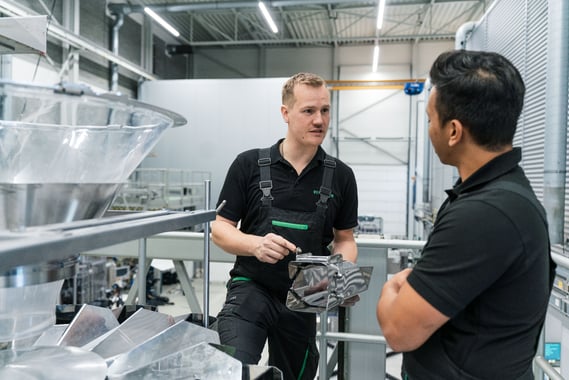
Service Agreements
Find out more about our Service Agreements here.
Process robustness and high efficiency are the main requirements for high-quality granulation in a high-shear mixer. Our technology is based on the unique Gentlewing impeller. The high-shear mixer granulator provides perfect mixing in short time and allows for a wide process window in terms of e.g. tip speed, filling level and mixing duration. At the same time, wall caking and product residues are minimized. The equipment’s intelligent features facilitate safe product transfer via a wet mill into the fluid bed, avoiding operator intervention. For older, already registered formulations, a traditional 3-blade impeller is available.
The Hüttlin Gentlewing is designed to achieve superior mixing and granulation results. The impeller’s shape matches the contour of the mixing container, while its angled blades ensure forced high-shear mixing of the product.
The prolonged blades further avoid wall caking, resulting in a higher yield.
You have the option to choose between the innovative Gentlewing impeller and a traditional 3-blade impeller for older formulations, which are already registered with this technology.
Our technology is available in a top (HTG) or bottom drive (HBG) execution.
Both share the same geometry, resulting in no process difference between top and bottom drive, achieving consistent high-quality results. The Gentlewing’s design and the vertical chopper support a high batch variability of 20 – 80 %.
Besides time and current measurement, we can additionally offer torque measurement to determine the end point of granulation as a validatable end point value.
Depending on your products’ characteristics and your plant’s layout, you can choose between different charging options: pneumatically by continuous or intermittent vacuum or alternatively by gravity filling. Especially for critical products, intermittent vacuum drastically reduces the filter load during charging.
In both our top and bottom drive executions, the Gentlewing and chopper shafts are equipped with a purged sealing system. The product container’s lid features an inflatable seal as well as an interlocking device to avoid cross-contamination. It further ensures product and operator safety.
The wall installation enables a true separation of the GMP and technical area, reducing the required space in the pharma room. All drives and supply lines are accessible via the technical area for time-efficient and safe maintenance.
The Hüttlin single pot combines all benefits of the leak-tight top-drive concept with a smart, efficient energy transfer via heated bowl, lid, filter housing and shaft, as well as an optimized vacuum system with optional solvent recovery. This concept meets the highest requirements regarding process times, product quality and handling.
Efficiency is one of the main benefits of our cleaning systems. Depending on your requirements, you can flexibly choose either our basic automated cleaning system or the advanced automated UltraClean technology. Thanks to its in-place cleaning, the UltraClean stainless-steel filter significantly reduces cleaning times and ensures reproducible results.
Are you looking for a small R&D tabletop mixer?
Mycromix granulates small amounts of products. Due to interchangeable bowls of 0.5, 1.0, 2.5, 5.0 and 10 liters, you can process a wide range of batch sizes. Mycromix features the same unique Gentlewing impeller and vertical chopper as our production-scale high-shear mixers. Mycromix is available with various options, such as preparation for organic solvents, heating/cooling jackets or a 3-blade impeller. In case you are seeking to expand your R&D capabilities, our Solidlab 1 and Solidlab 2 Plus fluid beds for drying perfectly complement the Mycromix table-top solution.
Unlike most other solutions in the market, the Solidlab 1 comes with our PROVICON control system featuring open recipe creation and management for a time-saving product development.
Would you like to run a small-scale production with a high-shear mixer?
Pilotmix is the perfect link between R&D and production scale: it can serve either as scale-up step between laboratory and production or as small production unit. It features the unique Gentlewing impeller as well as the proven vertical chopper. Options include single pot solutions, solvent recovery as well as a 3-blade impeller. Pilotmix is designed for customized containment upgrades to handle high-potent APIs. You can operate it either stand-alone, or in line with a Pilotlab fluid bed. PROVICON, our intuitive state-of-the-art controls completes the system.
Are you aiming to flexibly granulate with a high-shear mixer?
Our Hüttlin Top-/Bottom Drive Granulators (HTG/HBG) stand out with high efficiency and can process a large batch capacity of up to 1,800 liters. Our high-shear mixers are available as top or bottom drive execution. They feature the unique Gentlewing impeller as well as the vertical chopper. Options include single pot solutions, solvent recovery as well as a 3-blade impeller. Their design further allows customized containment upgrades to handle high-potent APIs. You can operate the HTG/HBG stand-alone or in line with a HD/HDG/HDGC fluid bed processor. PROVICON, our intuitive control system completes the system.
Are you looking for a lean and compact granulation line?
The compact Hüttlin GranuLean unit comprises a high-shear mixer, a wet mill, a fluid bed system, a dry mill as well as adequate material handling. Due to its small footprint, our granulation line can be easily integrated into new and existing pharmaceutical plants. The system comes in four pre-configured sizes and allows for shorter delivery times and faster ramp-up to production. It features the unique Gentlewing impeller as well as the vertical chopper and can optionally be equipped with a 3-blade impeller.
Whether you compress granules into tablets or fill them into capsules or sachets, e.g. for nutraceuticals – our high-shear mixer means outstanding quality for any dosage form.
Outstanding granule properties like smooth flowability and an ideal particle size distribution result in excellent compression characteristics– even at very low API concentration, e.g. for cancer therapy.
Effervescent tablets support easy oral administration, but prove challenging in terms of production. Our sophisticated single pot system is perfectly suited to produce granules for highly stable effervescent tablets.
Granules, pellets, and mini tablets are perfectly suited for fixed-dose or personalized combination capsules, e.g. anti-infective drugs. Our fluid bed granulators ensure optimum quality of the individual components.
Mycromix | Pilotmix | HTG | HBG | GranuLean | |
Product container volume (l) | 0.5 – 10 | 25 – 150 | 300 – 1,800 | 150 – 1,200 | 150 – 1,200 |
Batch range (kg) | 0.1 – 3.5 | 2.5 – 60 | 30 – 720 | 15 – 480 | 15 – 480 |
At a density of (kg/l) | 0.5 | 0.5 | 0.5 | 0.5 | 0.5 |
Find out more about our Service Agreements here.
Find out more about Digital Solutions here.
Find out more about Parts here.
Find out more about Maintenance here.
Find out more about Technical Support here.
Find out more about Modernizations here.
Find out more about our Training here.
Find out more about our Expert Services here.
Oral solid dosage forms (OSD) are our specialty: in the course of our long business history, we have been supporting countless industry players across the globe and sharing our rich expertise in high-shear mixing. As an innovation-driven company, we are far from maintaining the status quo: over the last few years, we have been actively pursuing new ways to advance OSD manufacturing. Download our selection of brochures to find out more.
Oral solid dose (OSD) manufacturing is a demanding endeavor. There is no better partner to tackle those tasks with than Syntegon. Our OSD services and process technology will make your production a rock-solid success. Find out more in this video.
Industry requirements and containment solutions for OSD forms
Join us at FCE Pharma, Latin America's largest pharmaceutical event! Visit Syntegon at booth C-80 from June 10-12, 2025, to discover our latest innovations
Discover Syntegon, a leader in vaccine manufacturing equipment with over 30 years of experience and...
Join us at Pharmatag 2025 in Crailsheim, Germany, and experience how co-creation revolutionizes...
Stay informed about the booming RTU syringe market and Syntegon's AIM DIRect, featuring...
Discover the TPR tablet compression range from Syntegon, a trusted name in OSD drug manufacturing...
Granulation is a core step for the production of OSD (oral solid dosage) products, mostly tablets and capsules.
Granules can be applied directly in sachets, be compressed to tablets, or filled into capsules.
The process step of granulation leads to:
There are several granulation methods available, including: Dry granulation with e. g. a roller compactor, and wet granulation in e. g. a high-shear mixer or a fluid bed processor (spray granulation). Each option offers benefits and limitations that need to be considered when selecting the optimal solution.
Dry granulation with e. g. a roller compactor does not require binding agents and drying. Powders are compressed into a ribbon and then milled into granules (de-agglomeration). However, dry granulation is not suitable for all types of recipes. Moreover, the characteristics of the starting materials must meet very narrow specifications to achieve consistent end results. This can pose additional challenges in terms of starting material sourcing during the life cycle of a drug product.
In a wet granulation process with e. g. a high-shear mixer, different powders are mixed to achieve a homogeneous blend. In the next step, a binder liquid is sprayed into the mixture which leads to the formation of liquid bridges between the particles. The impeller mixes the wet mass and forms granules by introducing shear force into the material. Additionally, a chopper is used to reduce oversized lumps into smaller pieces. High shear forces achieve a beneficial increase in granule density. The right endpoint of this process step can be determined e. g. by torque measurement, a method that allows for highly precise and repeatable results. At the end of the wet granulation process, the product is discharged from the high-shear container, sized in a wet mill, and dried e. g. in a fluid bed.
Spray granulation in a fluid bed processor starts by mixing the different powders until a homogeneous mixture is achieved. Spray guns then add the granulation liquid to the fluidized mixture. From a design perspective, the spray nozzles can be arranged in different ways (top, tangential, bottom). To achieve high density and a narrow particle size distribution it is beneficial to spray in the area where particles have the highest kinetic energy, i. e. directly above the air distribution plate that is positioned at the bottom of the fluid bed vessel. A controlled spray rate as well as stable droplet sizes via controlled spray parameters are essential to achieve repeatable results.
Drying of the granules already starts during the spraying step via the conditioned process air. The end of the drying step can be determined very precisely, e. g. by humidity measurements of the exhaust air.
Another key element of spray granulation is to keep the conditioned air in a consistent range of temperature, humidity, and mass flow to achieve repeatable results - independently from regional and seasonal fluctuations in the outside air drawn in.
To achieve repeatable granulation results in a high-shear mixer, here are some factors that need to be considered, including:
A high-shear mixer is a machine to produce granules using a wet granulation process:
Depending on the position of the driving shaft, one can distinguish between bottom-drive and top-drive technology high-shear mixers. Each design offers its advantages. The bottom-drive design has a fixed bowl and lid for easy container access. Top-drive high-shear mixers, in contrast, are equipped with a movable bowl and a fixed lid, which makes them fully accessible for cleaning validation.