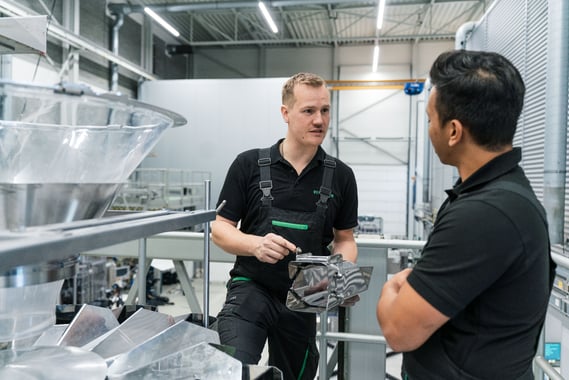
Service Agreements
Find out more about our Service Agreements here.
Our systems for thawing frozen blood plasma ensure gradual thawing of shear-sensitive products.
Based on decades of experience, Syntegon offers efficient systems for the synthesis and formulation of plasma derivatives, vaccines, and oncology products.
Syntegon inspection systems cover visual inspection and leak testing (CCIT) – from inline to end-of-line solutions.
Thanks to flow-optimized systems, our pasteurizers ensure consistently stable temperatures during final pasteurization of plasma derivatives.
Our flexible platforms ensure safe filling of sensitive proteins in the low, medium, and high output range.
Our freeze dryers ensure homogeneous temperatures, while the patented loading and unloading system enables precise processing and lyophilization.
Syntegon offers proven ultrafiltration, depth filtration, and chromatography systems to support the separation of blood plasma. We provide a comprehensive portfolio of viral inactivation and final purification options, including thermal inactivation and multi-stage enzyme purification.
Our customers process some of the most valuable and urgently needed pharmaceutical liquids, for example the new Covid-19 vaccines, oncology preparations or other biopharmaceutical drugs on our lines 24/7. Are you also looking for a reliable, safe, and efficient solution for your liquid vials? From stand-alone machines to entire lines – we are your experienced partner!
Purified media are a prerequisite for processing and producing liquid pharmaceuticals. Our portfolio includes both distillation and cold membrane processes for WFI, as well as thermal generation solutions for WFI and pure steam. Of course, we also offer you a well-designed system concept for the storage and distribution of PW and WFI. Our formulation systems, in turn, support you in producing the actual solutions. From preparation and filtration to centrifugation and chromatography – ask our experts and they will be sure to propose the right solution for your products.
Sterility matters across the entire aseptic process – before, during and after sterile filling. Syntegon offers internal and external cleaning machines for vials and other containers. Once the vials have been pre-cleaned with Water for Injection (WFI), our HQL tunnel ensures safe and reliable sterilization and depyrogenation with dry heat. Following filling and capping, the vials can be transferred to our RAN external cleaning machine, which makes sure that no particles adhere to the outer sides of the vials; an important factor in protecting operators and healthcare workers
Our vial filling systems combine flexibility and precision: a wide range of technologies, including valve piston and peristaltic pump, mass-flow, rolling diaphragm pump, time-pressure filling – or a combination of all within our combi filling station. Every filling system makes sure you can fill your products in a highly customized way. Tool-less format changes and filling stations with a variable number of filling heads increase the flexibility of your filling processes. Subsequent sealing offers you a variety of methods such as pick and place or continuous stoppering – without the use of vacuum. Continuous capping with high speeds completes the safe and reliable closing process. Quality will be increased with constant checks of filling weight by 100% check weighing systems (IPC) and inline inspection systems as empty vial inspection, stopper position control, crimp quality, cap roundness, print check - or whatever is required to control. Fully integrated into Syntegon machine control.
Aseptic filling is all about product safety – and thus the separation of operators and pharmaceutical ingredients. Isolator technology helps to build this crucial barrier. Syntegon has established a comprehensive portfolio, including open RABS, closed RABS, containment and isolator systems. All solutions are tailored to customer requirements, from machine design and development to on-site installation and validation.
Telstar's pharmaceutical freeze dryers offer unmatched quality with the perfect mix of standardization and customization. With multiple configurations available, there will be a solution that fits your needs. The Telstar brand has experience managing a wide range of container sizes and formats which guarantee the best production assurance. Our freeze dryers are ideal for small and large batch production: from 1 to 60 m2, under isolator or RABS, and connecting with filling lines with different loading and unloading solutions.
Benefits:
SBM (Schoeller-Bleckmann Medizintechnik) offers a vast portfolio of versatile sterilization solutions for an effective treatment of porous loads and liquids in open, semi-sealed or closed containers. The vacuum-steam, steam/air mixture and hot water shower processes support you in achieving reproducible equipment and terminal sterilization while optimizing your energy requirements
Inspection is a key quality safeguard for pharmaceuticals and contributes significantly to patient safety. It can also help to improve the entire production process. Our wide range of manual, semi and fully automated inspection machines inspects liquid and lyophilized pharmaceuticals for particles and container defects. Thanks to our long-standing inspection expertise, we offer state-of-the-art technologies for visual inspection and container closure integrity testing (CCIT), including high voltage leak detection (HVLD), static division (SD) and headspace analysis (HSA). During the filling process, inline inspection systems for empty vials, stopper position or crimp quality further increase product quality.
Find out more about our Service Agreements here.
Find out more about Digital Solutions here.
Find out more about Parts here.
Find out more about Maintenance here.
Find out more about Technical Support here.
Find out more about Modernizations here.
Find out more about our Training here.
Find out more about our Expert Services here.
Discover Syntegon, a leader in vaccine manufacturing equipment with over 30 years of experience and...
Explore Syntegon's transition from Waiblingen to new locations, setting the stage for future growth...
Join us this June for our OSD Academy expert seminar “Granulation – from powder to tablet”.
Learn more about our sustainable coffee packaging solutions.