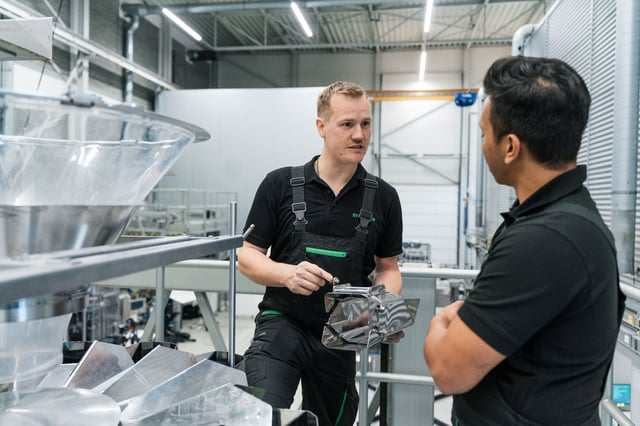
Service Agreements
Find out more about our Service Agreements here.
Whenever glass containers are at play, production processes become challenging. Glass ampoules are no exception: cleaning, filling, closing and inspecting the much-used containers require care and precision. At Syntegon, we have a passion for both: our ampoule filling and sealing machines for low to high-output production ensure gentle, hygienic and accurate processing. Different burning stations, filling technologies and handling systems allow us to tailor our systems to your production settings. Our portfolio enables us to easily combine all machines with upstream and downstream equipment such as barrier systems, effectively supporting your entire production line.
When it comes to bioprocessing, the systems from Syntegon’s subsidiary Pharmatec flexibly support the production of small and large volume parenterals (SVP/LVP) and infusions (IV). The process solutions comprise modular set-ups of temperature-controlled stainless-steel tanks that can be assembled to meet customer-specific settings. The new, cost-efficient SVP Essential is a fully automated, ready-to-use system to produce simple parenterals such as analgesics, insulin, and generic drugs.
Benefits:
Before and after filling, vials, ampoules, syringes, and cartridges need to undergo a crucial process step. Thorough internal and external cleaning is necessary to remove product residues and other contaminants from the containers’ inner and outer sides. As such, cleaning prevents potentially harmful substances from compromising operator and patient safety. Syntegon’s portfolio of compact pharmaceutical cleaning systems for the low, medium and high output ranges support manufacturers in reaching this goal. The hygienic and ergonomically designed solutions allow to clean a wide variety of containers, with special emphasis on fast and easy operations.
Benefits:
Whether you are filling liquid pharmaceuticals into ampoules, vials, injection and infusion bottles, cartridges or syringes: the reliable pre-treatment of containers significantly contributes to product safety. Thanks to a wide range of depyrogenation tunnels and related sterilization technologies, we provide versatile solutions for an effective and sustainable pre-treatment of liquids in open, semi-sealed or closed containers. Dry heat, vacuum, steam/air mixture and hot water shower sterilization help you achieve reproducible treatment quality while optimizing your energy requirements.
Benefits:
Our filling systems for pre-sterilized packaging combine flexibility and precision: a wide range of technologies, including valve piston and peristaltic pump, mass-flow and time-pressure filling, make sure you can fill your products in a highly customized way. Tool-less format changes and filling stations with a variable number of filling heads increase the flexibility of your filling processes. Subsequent sealing is equally versatile, offering you a variety of methods such as gas burning or vacuum stopper insertion for tightly sealed containers. In-process control (IPC) further improves filling quality with constant checks of filling weight and stopper location.
Benefits:
Like any pharmaceutical container, ampoules require thorough inspection to ensure patient safety. Our wide range of manual, semi and fully automated inspection machines inspects liquid and lyophilized pharmaceuticals for particles and container defects. Thanks to our long-standing inspection expertise, we offer state-of-the-art technologies for visual inspection and container closure integrity testing (CCIT), including high voltage leak detection (HVLD), static division (SD) and headspace analysis (HSA). Moreover, Syntegon provides fully integrated inline inspection solutions for several inspection tasks such as the detection of container defects.
Benefits:
The Syntegon company SBM (Schoeller-Bleckmann Medizintechnik) offers a vast portfolio of versatile sterilization solutions for an effective treatment of porous loads and liquids in open, semi-sealed or closed containers. The vacuum-steam, steam/air mixture and hot water shower processes support you in achieving reproducible equipment and terminal sterilization while optimizing your energy requirements.
Benefits:Are you looking for a compact, small-batch ampoule filling and sealing machine? Check out the ARF. The intermittent, rotary filling and closing machine reliable fills and seals different types at outputs of up to 6,000 containers per hour – with more than just one set-up. You can either process open and closed ampoules or vials, but also both packaging materials on the same machine. No matter which version you choose, the ARF 1000 stands for reliable, first-class results and offers optional 100 % IPC.
Benefits:
Ease of use at high outputs are key characteristic of our ALF 4000 filling and closing machine. As a linear, indexing-motion system, it fills and closes ampoules in the 1 to 30 milliliter volume range. With an output of up to 30,000 containers per hour, the ALF 4000 is not only capable of operating at high production rates. The secure system further supports gentle container handling and precise filling using various filling systems. It is simplified designed makes the ALF 4000 particularly easy to retrofit and provides excellent accessibility for maintenance and cleaning.
Benefits:
Three different versions for high-output production: this sums up what the ALF 5000 has in store for you. The latest generation of the proven ALF series of filling and closing machines achieves high outputs of up to 36,000 ampoules or vials per hour. You can choose to either process open and closed ampoules or vials, but also both packaging materials on the combi platform. The improved pharmaceutical design and accessibility make the ALF 5000 a benchmark in the high-performance range. Hygienic operations are another mainstay, as the easy-to-clean machine shows a lower contamination tendency.
Benefits:
Find out more about our Service Agreements here.
Find out more about Digital Solutions here.
Find out more about Parts here.
Find out more about Maintenance here.
Find out more about Technical Support here.
Find out more about Modernizations here.
Find out more about our Training here.
Find out more about our Expert Services here.
Our solutions for processing ampoules
Join us at Pharmatag 2025 in Crailsheim, Germany, and experience how co-creation revolutionizes tomorrow’s pharmaceutical processes.
Stay informed about the booming RTU syringe market and Syntegon's AIM DIRect, featuring...
Discover the TPR tablet compression range from Syntegon, a trusted name in OSD drug manufacturing...
Join us at Pack Expo in Chicago from November 3-6! Discover Syntegon's solutions in the Healthcare...
Meet our experts at CPHI in Milan from October 8 to 10, 2024. Learn more about Syntegon's...