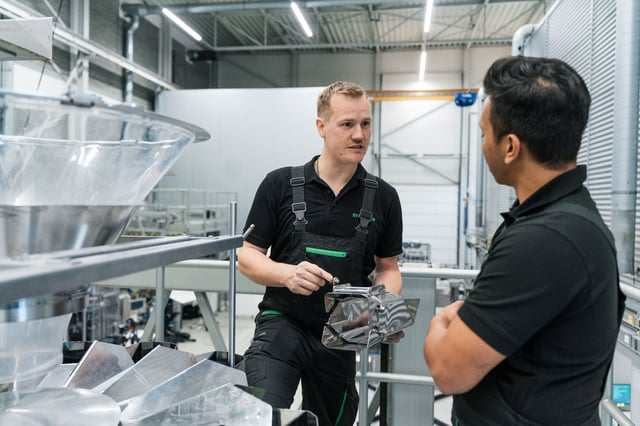
Service Agreements
Find out more about our Service Agreements here.
Pharmaceutical manufacturers have been trusting Syntegon for more than 60 years to process their vials reliably, safely, and efficiently. We have installed more than 1,500 vial filling machines all over the world. They are used to process some of the most valuable and urgently needed pharmaceutical liquids in 24 hour operations, for instance the new Covid-19 vaccines, oncology preparations or other biopharmaceuticals. Either as a classical bulk process with washing and depyrogenation tunnel, or in combination with ready-to-use (RTU) vials in trays – we support you with our comprehensive knowledge and technical solutions.
The perialistic pump, for example, is a displacement pump, which presses the product through the filling hoses by means of mechanical hose deformations.
Our Combi filling station is a highly flexible filling platform, which enables you to use multiple filling technologies and dosing units in a small space. Start with one filling system and retrofit with another or even more, just as your projects require.
During the filling process, inline inspection systems for empty vials, stopper position or crimp quality further increase product quality and maximize product yield.
Our KIV facilitates the tracking and identification of each filled and sealed vial and brings benefits in product safety. Protection against counterfeiting is especially successful when combined with SODA for single object data coding of every single vial within the primary packaging process.
Our machines all feature a clean and hygenic design for easy cleaning operations and the highest operator safety.
The FLC 3000 has set trends and delivered proof in many customer applications: its unique combination of flexibility and compact design have made it the preferred choice for safe and efficient filling and closing of vials and infusion bottles in the medium and high output range: 600 vials per minute are possible with a filling range of 0.2 to 500 milliliters. This is achieved with only three format part sets and minimal changeover times. No pharmaceutical filler was built more often as the FLC – with more than 650 installations worldwide.
Benefits:
Three different versions for high-output production: this sums up what the ALF 5000 has in store for you. The latest generation of the proven ALF series of filling and closing machines achieves high outputs of up to 36,000 vials or ampoules per hour, or both on the combi platform. The improved pharmaceutical design and accessibility make the ALF 5000 a benchmark in the high-performance range. Hygienic operations are another mainstay, as the easy-to-clean machine shows a lower contamination tendency. It further features an optional 100 % in-process control (IPC) at constant speeds.
Benefits:
The MLF 300 filling and closing machine for vials and infusion bottles combines medium output with the highest flexibility. Its modular design and large processing range from 2 to 500 milliliters make it ideally suited for versatile applications. You can achieve output rates up to 200 containers per minute. Monoblock versions including crimping in a capsuled design are also available, still featuring a small footprint.
Benefits:
If you are looking for a flexible filling and closing machine for industrial small-scale production and studies of pharmaceutical liquids in vials, our ARF 1000 is the right choice. The intermittent, rotary machine achieves an output of up to 6,000 containers per hour. You receive the highest flexibility and efficiency combined with a small footprint. The optional 100 % in-process control (IPC) adds to safe and reliable results. We also offer a monobloc version with integrated or separated capping including inline inspection systems. And for everyone looking for even more flexibility: the ARF is also available as a combi machine for vials and ampoules in the smallest space.
Benefits:
Highly potent, personalized pharmaceuticals mean small patient populations – and equally small batch sizes. As a highly standardized and modular solution, the Versynta Flexible Filling Platform (FFP) enables manufacturers to approach aseptic filling in a new way.
Benefits:
Just like small batch production, micro batch manufacturing is coming to the fore of everyday pharmaceutical operations. Together with a customer, we are currently testing the second instalment of the Versynta portfolio, the gloveless microBatch working cell.
Benefits:
Find out more about our Service Agreements here.
Find out more about Digital Solutions here.
Find out more about Parts here.
Find out more about Maintenance here.
Find out more about Technical Support here.
Find out more about Modernizations here.
Find out more about our Training here.
Find out more about our Expert Services here.
Pack style cracks: vials or bottles come in different shapes and sizes – and with specific challenges. We help you find the matching processing equipment.
Customizable solutions: modularity is a built-in characteristic of our bulk processing solutions. They perfectly blend into your production environment.
Full process expertise: from filling to closing and freeze drying, we have got you covered with a comprehensive portfolio.
Learn more about our vial liquid portfolio
Together in the fight against Covid-19: our complete vaccine production systems at a glance
An industry-first series of experiments to investigate Vaporized Hydrogen Peroxide (VHP) decontamination
Join us at Pharmatag 2025 in Crailsheim, Germany, and experience how co-creation revolutionizes tomorrow’s pharmaceutical processes.
Stay informed about the booming RTU syringe market and Syntegon's AIM DIRect, featuring...
Discover the TPR tablet compression range from Syntegon, a trusted name in OSD drug manufacturing...
Join us at Pack Expo in Chicago from November 3-6! Discover Syntegon's solutions in the Healthcare...
Meet our experts at CPHI in Milan from October 8 to 10, 2024. Learn more about Syntegon's...