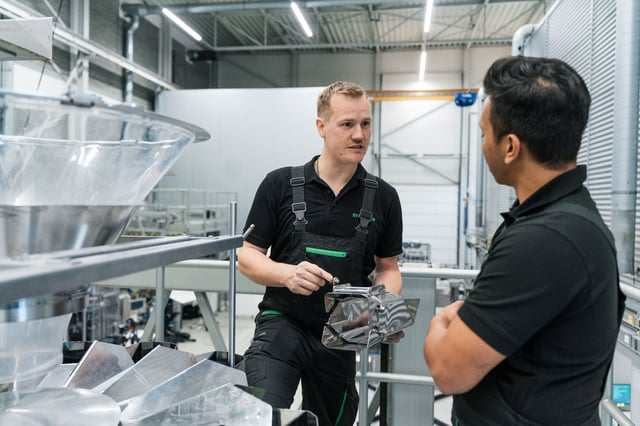
Service Agreements
Find out more about our Service Agreements here.
Syntegon capsule filler
Our automatic capsule filling machine series provide best conditions for highest pharmaceutical standards – from R&D and pilot scale to high production volumes. Whether you need to fill powders, (mini-) tablets, pellets, granules, liquids, or different combinations into hard shell capsules (HPMC or gelatin capsules), we offer you the appropriate process technology for the production of both pharmaceutical and health and nutrition products (supplements). We also provide a containment concept for several capsule filling machine platforms for the production of potent APIs up to OEB 4 or OEB 5, which ensure the highest operator protection.
Syntegon is your reliable partner for process technology in the global pharmaceutical industry. We offer you solutions for all requirements – from R&D and pilot scale to high volume production, based on more than 50 years of experience as a capsule filling machine manufacturer.
The future-proof GKF Performance series features highly flexible capsule filler machine platforms that ensure the highest pharmaceutical production standards. Based on more than 50 years of experience as a capsule filling machine manufacturer, the machines are designed to facilitate complex dosing processes and are equipped with fully integrated inspection technologies. The GKF Performance series is capable of filling different types of products or combinations into hard shell capsules (HPMC or gelatin capsules). All capsule fillers of the Performance series are also available with the Syntegon ProTect and HiProTect containment concept for highest operator protection.
The GKF Selection series provides best conditions for modern, flexible, and safe capsule filler operations. All machines are capable of filling different types of products or combinations into hard shell capsules (HPMC or gelatin capsules). Thanks to their modular assembly, the capsule fillers can accommodate applications for (mini-) tablets, pellets, granules, liquids, or combinations. Quick changeover times and intuitive handling make the GKF Selection series your ideal choice for the production of both pharmaceutical and health and nutrition products (supplements).
Containment is all about operator safety. The product area is separated from the personnel area by a barrier system to prevent any negative impacts (contamination). Syntegon provides two different solutions for OSD (Oral Solid Dosage) processing under containment conditions: the ProTect (up to OEB 4) and HiProTect (up to OEB 5) execution. We further offer three different cleaning approaches for closed capsule filler machines, which you can adapt to your specific needs together with our experts.
The GKF Capsylon machine series is specially designed for the nutrition and health industry (supplements). It provides the renowned Syntegon quality at an excellent price-performance ratio. The capsule fillers are suited for the filling of powders, pellets and granules into various capsule sizes. They meet the growing need for high efficiency, easy operation, and simple cleaning. The GKF Capsylon machine series is the ideal solution to increase your production capacity while reducing unit dosage costs.
Find out more about our Service Agreements here.
Find out more about Digital Solutions here.
Find out more about Parts here.
Find out more about Maintenance here.
Find out more about Technical Support here.
Find out more about Modernizations here.
Find out more about our Training here.
Find out more about our Expert Services here.
Discover our solutions for mixing, drying, granulating, coating, capsule filling, and tablet pressing.
Our R&D equipments
A sophisticated approach to laboratory automation.
Join us at Pharmatag 2025 in Crailsheim, Germany, and experience how co-creation revolutionizes tomorrow’s pharmaceutical processes.
Stay informed about the booming RTU syringe market and Syntegon's AIM DIRect, featuring...
Discover the TPR tablet compression range from Syntegon, a trusted name in OSD drug manufacturing...
Join us at Pack Expo in Chicago from November 3-6! Discover Syntegon's solutions in the Healthcare...
Meet our experts at CPHI in Milan from October 8 to 10, 2024. Learn more about Syntegon's...
Syntegon’s in-house OSD Customer Center provides the entire processing infrastructure, from clean room facilities to equipment for processing trials. The Customer can perform the trial themselves or have the Syntegon process specialists perform the trials for them. Customers can bring their own capsules or use empty capsules provided by Syntegon for the machine trials.
The capsule filling process on our GKF capsule fillers involves several steps
Different types of components and component combinations can be dosed on our GKF capsule filling machines:
Powder: Dosing station with optimized slide-gate technology for the filling of powders, granules, and pellets.
Pellets: The pellet station is a gentle, precise, and compact option for the volumetric dosing of pellets with different characteristics.
(Micro) Tablets: The tablet station doses single and multiple tablets into capsules gently and precisely – from large oblong to micro-tablets.
Micro-Dosing: Vacuum-wheel dosing is especially suited for dry powder inhalation (DPI) and active pharmaceutical ingredient (API) dosing with a high accuracy for small quantities.
Liquids: The liquid station enables the precise volumetric dosing of hydrophilic to thixotropic liquids. It can also heat liquids for optimum viscosity during the filling process.
Combinations: The GKF series can fill a wide array of product combinations thanks to its modular assembly. Various successful projects underline our expertise.
Specials: Capsule into capsule.
We offer a range of inspection technologies in our portfolio to meet your needs. Our portfolio of inspections technologies include:
KKE series: The KKE capsule checkweighing series sets the standard in 100 % capsule weighing. With its mechanical pre-dedusting system, the precise gravimetric weighing technology makes the KKE series the ideal choice for your capsule checkweighing needs. The platforms also answer the growing needs of the nutraceutical and health industry (supplements) in terms of process control and increases product quality in your capsule production. Need more information? Learn more about our KKE series here.
In-process control: The integrated gravimetric scale system ensures an automatic statistical capsule check weighing for low fill-weight capsules. It allows the Customer to analyze those capsules in real-time, improving quality and reducing waste.
Net-weight-detection system (NWDS): 100% net weight control system with weight determination via electromagnetic field sensor. During the dosing process, the dosing mass passes through a mass detection sensor. Here, the interruption generated in the sensor field is measured against a pre-set mass to weight reference that is set during an automated teach in process with the integrated IPC.
Process optimization technologies: