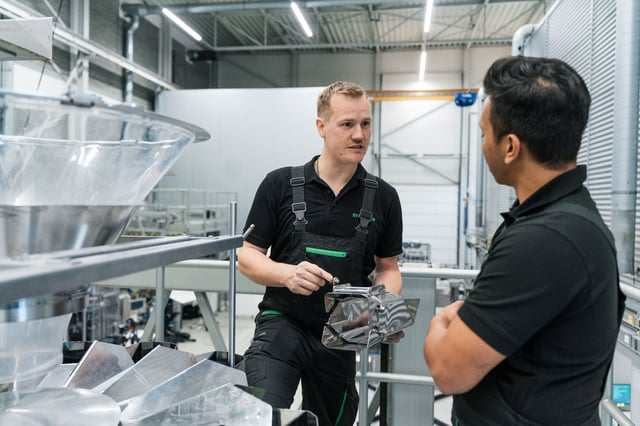
Service Agreements
Find out more about our Service Agreements here.
Performance meets precision in Syntegon’s cartridge filling and capping portfolio. Our solutions for all output ranges help you process cartridges at optimum conditions. From accurate positioning under the working stations to low-particle capping with patented technologies, our cartridge filling systems reliably support each step of your production cycle. High-quality operations are equalled by a modular and space-saving design, facilitating the integration into state-of-the-art production lines.
Cartridge processing is not just a production step – it’s a complex task that calls for support from a leading equipment manufacturer. If you are curious to find out why we are the undisputed number one in this field, explore our videos!
When it comes to bioprocessing, the systems from Syntegon’s subsidiary Pharmatec flexibly support the production of small and large volume parenterals (SVP/LVP) and infusions (IV). The process solutions comprise modular set-ups of temperature-controlled stainless-steel tanks that can be assembled to meet customer-specific settings. The new, cost-efficient SVP Essential is a fully automated, ready-to-use system to produce simple parenterals such as analgesics, insulin, and generic drugs.
Benefits:
Sterility matters across the entire aseptic process – before, during and after sterile filling. Especially highly potent and/or freeze-dried products pose a risk to operators and patients after filling, as product residues or contaminants on the containers’ outer wall might affect the health of personnel. Syntegon‘s external washing solutions keep the outside surfaces of filled and sealed containers clean: high-pressure nozzles wash off any excess product, while keeping the closures intact.
Benefits:
Whether you are filling liquid pharmaceuticals into ampoules, vials, injection and infusion bottles, cartridges or syringes: the reliable pre-treatment of containers significantly contributes to product safety. Thanks to a wide range of depyrogenation tunnels and related sterilization technologies, we provide versatile solutions for an effective and sustainable pre-treatment of liquids in open, semi-sealed or closed containers. Dry heat, vacuum, steam/air mixture and hot water shower sterilization help you achieve reproducible treatment quality while optimizing your energy requirements.
Benefits:
Our filling systems for pre-sterilized and bulk containers combine flexibility and precision: a wide range of technologies, including valve piston and peristaltic pump, mass-flow and time-pressure filling, make sure you can fill your products in a highly customized way. Tool-less format changes and filling stations with a variable number of filling heads increase the flexibility of your filling processes. Subsequent sealing is equally versatile, offering you a variety of methods such as gas burning or vacuum stopper insertion for tightly sealed containers. In-process control (IPC) further improves filling quality with constant checks of filling weight and stopper location.
Benefits:
Aseptic filling is all about product safety – and thus the separation of operators and pharmaceutical ingredients. Isolator technology helps to build this crucial barrier. With over 40 years of US-based and 25 years of German-based experience in the design and manufacture of barrier systems, Syntegon has established a comprehensive portfolio, including open RABS, closed RABS, containment and isolator systems. We focus on each component to make sure it seamlessly interacts with others: safe interfaces between filling machines, isolators and subsequent systems, e.g., freeze-dryers or capping machines are a top priority.
Benefits:
The Syntegon company SBM (Schoeller-Bleckmann Medizintechnik) offers a vast portfolio of versatile sterilization solutions for an effective treatment of porous loads and liquids in open, semi-sealed or closed containers. The vacuum-steam, steam/air mixture and hot water shower processes support you in achieving reproducible equipment and terminal sterilization while optimizing your energy requirements.
Benefits:
Like any pharmaceutical container, pre-filled syringes require thorough inspection to ensure patient safety. Our wide range of manual, semi and fully automated inspection machines inspects liquid and lyophilized pharmaceuticals for particles and container defects. Thanks to our long-standing inspection expertise, we offer state-of-the-art technologies for visual inspection and container closure integrity testing (CCIT), including high voltage leak detection (HVLD), static division (SD) and headspace analysis (HSA). Moreover, Syntegon provides fully integrated inline inspection solutions for several inspection tasks such as empty vial, crimping and stopper seat inspection.
Benefits:
Pens and cartridges are a winning team, provided they are assembled in an efficient, fully compliant way. Our modular assembly systems with scalable levels of automation make sure this is the case: they reliably support the production of standard 4-piece disposable pens and come in different designs according to your desired production rates. The rotary table version covers lower and medium outputs, while a linear transport system takes care of high-volume batches.
Benefits:
Bulk processing is a challenge of its own: the containers must be processed at high speeds, asking for reliable and fast operations. Our broad range of flexible cartridge filling machines makes sure you achieve the desired throughput at peak efficiency. Impressive processing ranges, simple changeover concepts and fully automated systems make sure you can reach this goal in a GMP-compliant way.
With decades of experience, we offer you a broad range of flexible syringe, cartridge and vial platforms, covering upstream and downstream processes. Our portfolio comprises systems that effectively support small, medium and high output production of liquid and lyophilized pharmaceuticals.
Versynta is our name for flexible small and micro batch filling operations. The Flexible Filling Platform (FFP) is ideally suited for small batches up to 3,600 containers per hour for vials, syringes, and cartridges, both bulk and RTU. The gloveless and fully robotized Versynta microBatch working cell processes aseptic and high-potent micro batches within a fully integrated machine and isolator unit.
Customers from around the globe rely on our cartridge filling and closing expertise. We have supported some of the most renowned industry players in boosting their efficiency, expanding operations or upgrading their equipment to meet latest manufacturing standards. Explore our customer cases to find out more about the many areas of application.
Find out more about our Service Agreements here.
Find out more about Digital Solutions here.
Find out more about Parts here.
Find out more about Maintenance here.
Find out more about Technical Support here.
Find out more about Modernizations here.
Find out more about our Training here.
Find out more about our Expert Services here.
Our solutions for processing cartridges
Join us at Pharmatag 2025 in Crailsheim, Germany, and experience how co-creation revolutionizes tomorrow’s pharmaceutical processes.
Stay informed about the booming RTU syringe market and Syntegon's AIM DIRect, featuring...
Discover the TPR tablet compression range from Syntegon, a trusted name in OSD drug manufacturing...
Join us at Pack Expo in Chicago from November 3-6! Discover Syntegon's solutions in the Healthcare...
Meet our experts at CPHI in Milan from October 8 to 10, 2024. Learn more about Syntegon's...