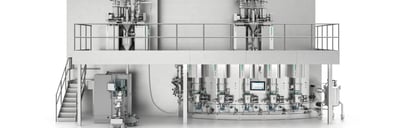
Continuous manufacturing of pharmaceuticals
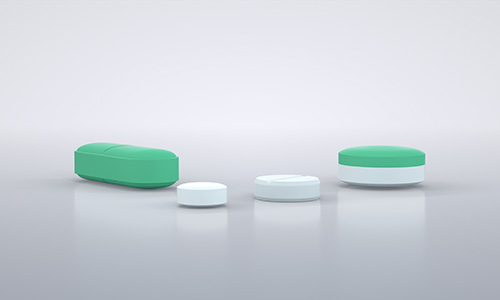
Pharmaceutical Continuous Manufacturing (PCM) is changing oral solid dosage (OSD) production. Higher flexibility, shorter development times with minimum API usage, and a direct transfer from development to production without scale-up are among the primary requirements of manufacturers in the pharmaceutical industry. In the continuous manufacturing of pharmaceuticals, the processes occur one after the other without interruption while the product is charged and discharged simultaneously. The main challenge with traditional solutions is the precise dosing of the starting materials in a constant mass flow rate of milligrams per second.
Syntegon is tackling the challenges in pharmaceutical continuous manufacturing with a different approach called Xelum.
Why choose continuous manufacturing?
Watch the video to learn more.
OSD: Many facets – one partner
Oral solid dose (OSD) manufacturing is a demanding endeavor. There is no better partner to tackle those tasks with than Syntegon. Our OSD services and process technology will make your production a rock-solid success. Find out more in this video.
Xelum: The fastest way to continuous manufacturing of pharmaceuticals
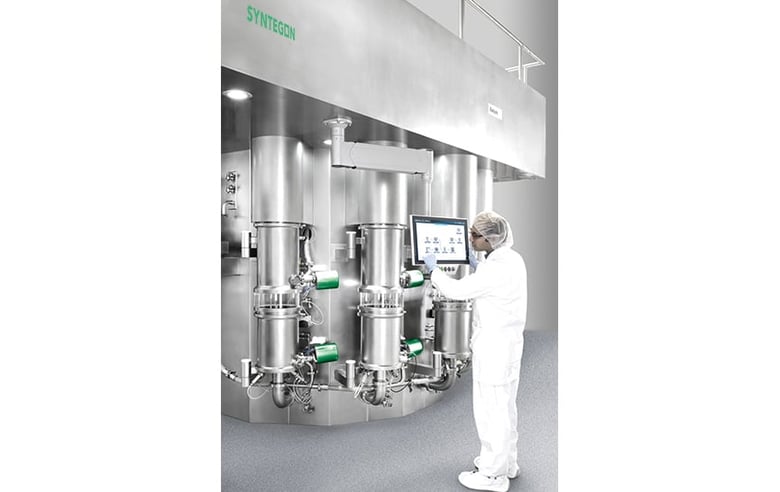
The Xelum platform for continuous manufacturing of pharmaceuticals doses active ingredients and excipients as discrete masses and not as a continuous mass flow. This way, even smallest amounts of APIs of less than 1% can be dosed precisely. The system doses, mixes and granulates individual packages, so-called X-keys, which continuously run through the process chain and are discharged successively as granules, tablets, or capsules.
Unique and proven technology
The Xelum platform is based on the robust and proven fluid bed processors that Syntegon has been refining for over 30 years for the pharmaceutical industry. They cover granulation and drying in the same process chamber. This eliminates the need to transfer wet granulate, benefitting the system’s reliability. Xelum achieves high granulation yields with the desired characteristics – including unimodal particle size distribution, as well as excellent flow and tableting properties. The platform further ensures lower production costs and high flexibility. The same holds true for the Xelum R&D and pilot unit, your point of entry into pharmaceutical continuous manufacturing.
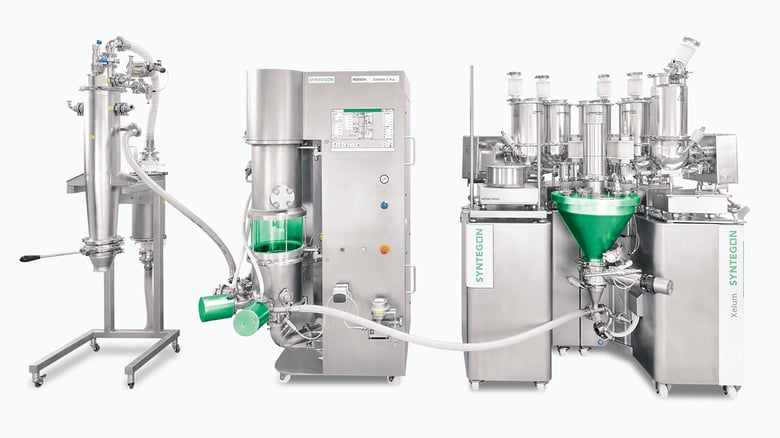
Xelum R&D and pilot line
Our Xelum R&D is your ideal start into continuous manufacturing of pharmaceuticals.
Since it uses exactly the same components as the Xelum production platform, process parameters can be directly transferred 1:1 without scale-up. This is valid for dosing, blending, and granulation. You can develop formulations for both batch and continuous manufacturing on the same machine, starting from 250 g. Xelum R&D can run clinical trial and pilot batches at a rate of 10 kg/h. The user-friendly controls of the continuous manufacturing system is complemented by a practical, automated DoE support. As a fully contained unit, it is also perfectly suited for the development of high potent APIs.
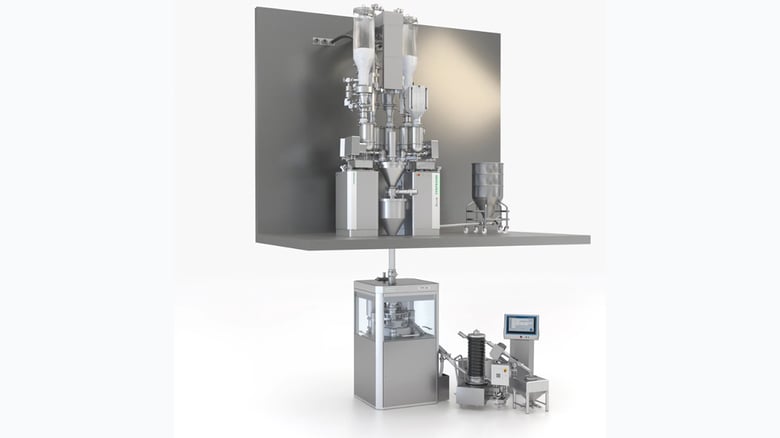
Xelum for continuous direct compression and encapsulation
With the Xelum production unit, all process parameters can be transferred 1:1 from the Xelum R&D since both machines share exactly the same components. This results into a material (API) and time saving scale-out to production - no scale-up required.
The Xelum allows for seamless continuous direct compression and encapsulation. It achieves throughputs of 50-100 kg/h, ensuring rapid manufacturing cycles. Xelum enables precise dosing down to 0.25% API concentration, maintaining exact formulation standards. It further provides containment capabilities for OEB4 materials with integrated WIP (washing in place).
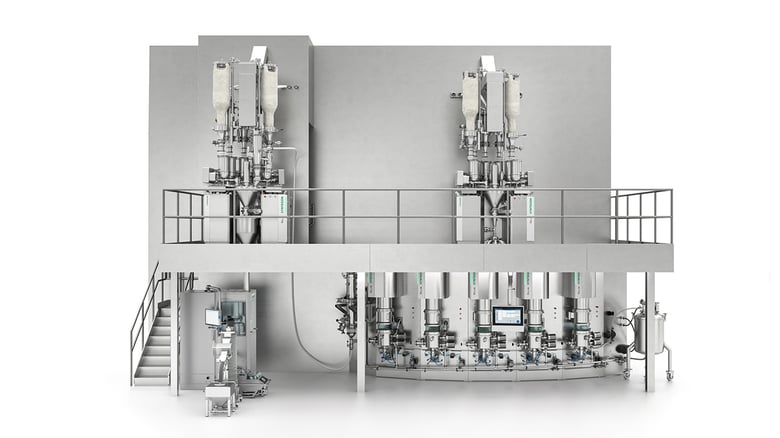
Xelum for continuous fluid bed granulation
Besides continuous direct compression, the Xelum also offers continuous fluid bed granulation with throughputs up to 30 kg/h. The granules offer excellent properties in terms of unimodal particle size distribution, flowability, compactability and content uniformity. APIs of less than 1 % can be dosed precisely.
Both tablet presses and capsule filling machines can be integrated for a comprehensive and streamlined manufacturing approach. It further provides containment capabilities for OEB4 materials with integrated WIP (washing in place).
Features of our continuous manufacturing platform

Simplicity
Our simplified process concept includes smart controls that keep your process within specification. They eliminate the need for complex measurement technology while ensuring consistently high product quality.
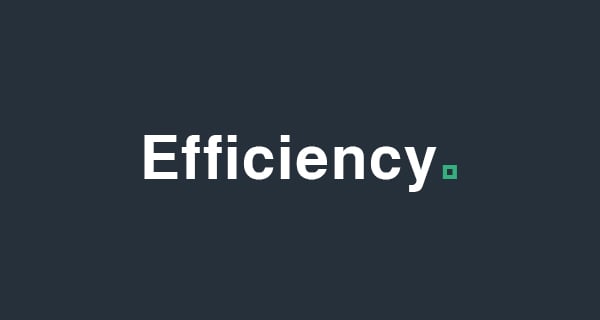
Efficiency
The Xelum platform for continuous manufacturing of pharmaceuticals facilitates precise dosing of even the smallest amounts of active pharmaceutical ingredient (API). Our innovation allows you to run robust processes with minimized start-up and shut-down losses, resulting in high yields. All individual product packages, so-called X-keys, are within specification – from the very first to the very last.
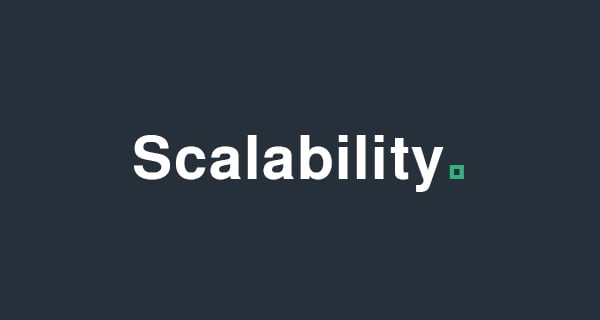
Scalability
Xelum continuous manufacturing technology allows you to save time and drastically cut costs, as direct process transfers from R&D to production don’t require scale-up.
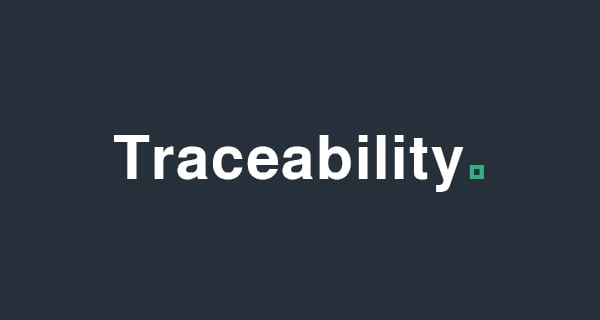
Traceability
X-keys stay fully separated from each other before they reach the tablet press or capsule filling machine. Each X-key has its own fingerprint, linking the final product with all critical process parameters, critical quality attributes and raw material lot numbers.
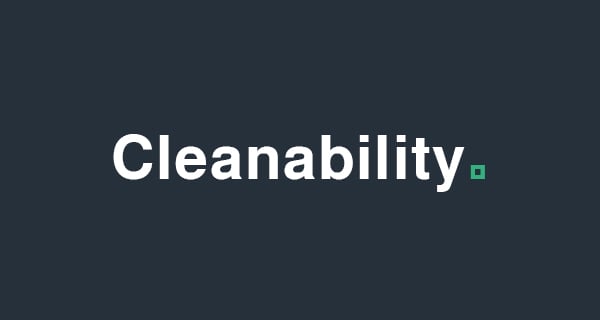
Cleanability
The design of our equipment is based on a thought-through cleaning concept from the very beginning. The automated cleaning process enables for fast cleaning in only one shift.
Use cases of our continuous manufacturing platform
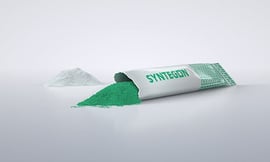
Outstanding granule quality
Whether you compress granules into tablets or fill them into capsules or sachets, e.g. for nutraceuticals – our Xelum for continuous manufacturing of pharmaceuticals achieves outstanding quality for any dosage form.
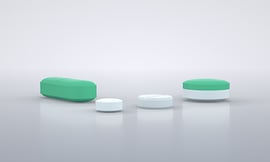
Tablets at their best
Outstanding granule properties like smooth flowability and an ideal particle size distribution result in excellent compression characteristics – even at very low API concentration, e.g. for cancer therapy.
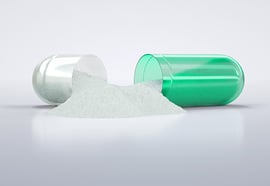
Yes, we capsule
Granules, pellets and mini tablets are perfectly suitable for fixed-dose or personalized combination capsules, e.g. anti-infective drugs. Our Xelum ensures optimum quality of the individual components.
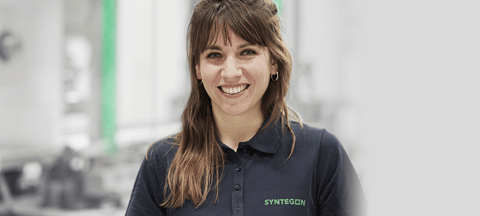
Technical data of our continuous manufacturing technology
Xelum R&D and pilot scale |
Xelum fluid bed granulation |
Xelum direct compression and encapsulation | |
---|---|---|---|
Throughput up to (kg/h) |
10 | 30 | 100 |
At a density of (kg/l) | 0.5 | 0.5 | 0.5 |
Continuous manufacturing downloads
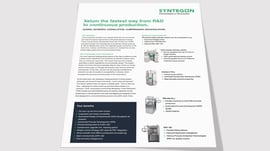
Xelum – from R&D to production
The fastest way from R&D to continuous production
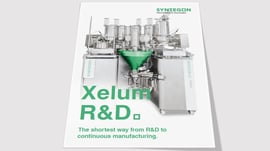
Xelum R&D
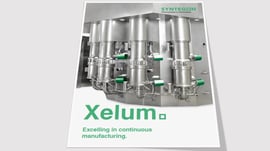
Xelum
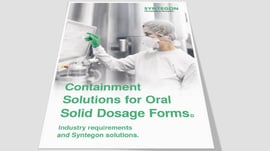
Containment Brochure
Industry requirements and containment solutions for OSD forms
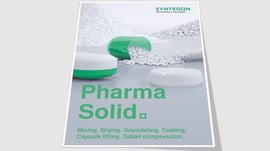
Pharma Solid
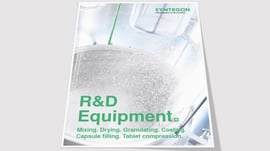
R&D Equipment
Our R&D equipments
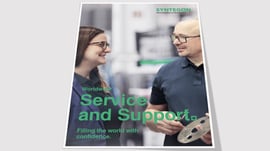
Hüttlin Services
Why choose our Xelum platform for pharmaceutical continuous manufacturing?
Expertise in the pharmaceutical industry
Oral solid dosage forms (OSD) are our specialty: in the course of our long business history, we have supported countless pharmaceutical industry players across the globe and shared our rich expertise in tablet coating. As an innovation-driven company, we are far from maintaining the status quo: over the last few years, we have been actively pursuing new ways to advance OSD manufacturing. Download our selection of brochures to find out more.
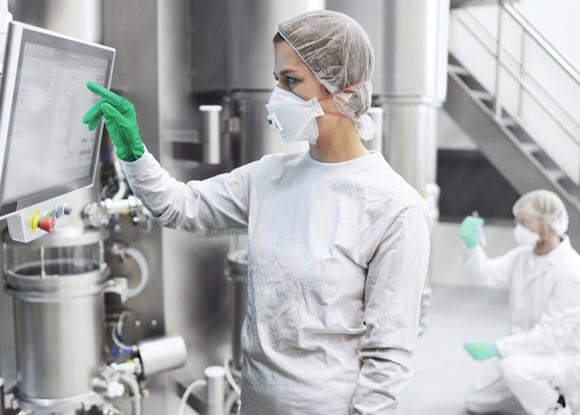
Syntegon enters strategic parnership with Bayer
The cooperation is based on the Xelum platform developed by Syntegon's subsidiary Hüttlin, which both partners intend to advance together and establish as a standard for continuous production in the pharmaceutical industry.
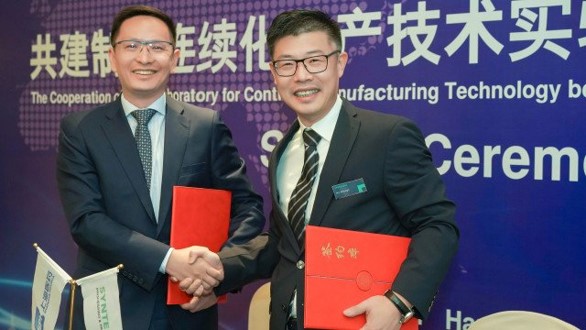
Shanghai Pharmaceuticals and Syntegon partner to promote continuous manufacturing in China
Shanghai Pharmaceuticals and Syntegon have signed an agreement to build a laboratory for continuous manufacturing technology in China. The cooperation will promote the application of this new technology, shorten development cycles of new drugs, reduce the cost of drug development, continuously improve the accessibility of new (especially orphan) drugs in China, and create more value for patients.